Preparation method of charcoal-based heat conduction rubber
A heat-conducting rubber and bio-char technology, which is applied in the field of preparation of bio-char-based heat-conducting rubber, can solve the problems of decreased mechanical properties of rubber products, low bonding degree, poor compatibility between bio-char and rubber, etc., and achieve surface activity and increased roughness , modified filling effect, good thermal conductivity and mechanical properties
- Summary
- Abstract
- Description
- Claims
- Application Information
AI Technical Summary
Problems solved by technology
Method used
Examples
Example Embodiment
[0019] Example 1
[0020] Weigh 1 kg of bamboo strips and grind and degum them in a corundum mortar for 1 hour, and then rinse the ground bamboo strips with 0.5mol / L hydrochloric acid for 2 hours and then dry them, and pickling the dried bamboos according to the solid-liquid ratio of 1:5 Mix the flakes with 1mol / L sodium hydroxide solution, shake and soak overnight on a shaker; after the end of immersion, the filter residue is obtained by centrifugal separation and placed in a Buchner funnel, filtered and washed with deionized water for 3 times, and the filter residue is naturally dried , Then put the dried filter residue into a carbonization furnace, heat it to 300°C under the protection of argon, heat it up to 300°C for 2 hours, and then grind it through a 100-mesh sieve to obtain bamboo-based biochar powder; weigh 100g peach gum and 500mL distilled water and mix Then put it into a beaker, move the beaker into a 60°C water bath and stir for 20 minutes to obtain a modified peac
Example Embodiment
[0022] Example 2
[0023] Weigh 2kg of bamboo strips and grind and degum them in a corundum mortar for 2h, and then rinse the ground bamboo strips with 0.5mol / L hydrochloric acid for 3h and then dry them. According to the solid-liquid ratio of 1:5, pickling the dried bamboo Mix the flakes with 1mol / L sodium hydroxide solution, shake and soak overnight on a shaker; after the end of immersion, the filter residue is obtained by centrifugal separation and placed in a Buchner funnel, washed with deionized water for 4 times, and the filter residue is naturally dried , Then put the dried filter residue into the carbonization furnace, heat it to 350°C under the protection of argon, and keep it carbonized for 3 hours, then grind through a 100-mesh sieve to obtain bamboo-based biochar powder; weigh 150g peach gum and 550mL distilled water and mix Then put it into a beaker, move the beaker into a 65°C water bath and stir for 25 minutes to obtain a modified peach gum solution. Mix the bambo
Example Embodiment
[0025] Example 3
[0026] Weigh 2kg of bamboo strips and grind and degum them in a corundum mortar for 2h, and then rinse the ground bamboo strips with 0.5mol / L hydrochloric acid for 3h and then dry them. According to the solid-liquid ratio of 1:5, pickling the dried bamboo Mix the flakes with 1mol / L sodium hydroxide solution, shake and soak overnight on a shaker; after the end of immersion, the filter residue is obtained by centrifugal separation and placed in a Buchner funnel, washed with deionized water for 5 times, and the filter residue is naturally dried , Then put the dried filter residue into a carbonization furnace, heat it to 400°C under the protection of argon, and keep it carbonized for 3 hours, then grind it through a 100-mesh sieve to obtain bamboo-based biochar powder; weigh 200g peach gum and 600mL distilled water and mix Then put it into a beaker, move the beaker into a 70°C water bath and stir for 30 minutes to obtain a modified peach gum solution. Mix the bamb
PUM
Property | Measurement | Unit |
---|---|---|
Thermal conductivity | aaaaa | aaaaa |
Tensile strength | aaaaa | aaaaa |
Tear strength | aaaaa | aaaaa |
Abstract
Description
Claims
Application Information
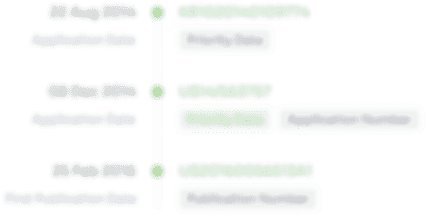
- R&D Engineer
- R&D Manager
- IP Professional
- Industry Leading Data Capabilities
- Powerful AI technology
- Patent DNA Extraction
Browse by: Latest US Patents, China's latest patents, Technical Efficacy Thesaurus, Application Domain, Technology Topic.
© 2024 PatSnap. All rights reserved.Legal|Privacy policy|Modern Slavery Act Transparency Statement|Sitemap