Preparation method of positive plate with pre-embedded lithium graphene
A positive electrode sheet and graphene technology, applied in hybrid capacitor electrodes, hybrid/electric double-layer capacitor manufacturing, electrolytic capacitors, etc., can solve the problems of difficult manufacturing process and complicated process, so as to lower the potential of the negative electrode, simplify the preparation process, cost reduction effect
- Summary
- Abstract
- Description
- Claims
- Application Information
AI Technical Summary
Benefits of technology
Problems solved by technology
Method used
Image
Examples
Embodiment 1
[0032] (1) Add 10g of graphite oxide and 0.001g of polyacrylonitrile into a ball mill and mill for 30 minutes, then add the ball-milled mixture into a mixed solution with a volume ratio of ethanol and water of 0.25 for ultrasonic dispersion to form a suspension with a concentration of 1g / L .
[0033] (2) Soak the nickel foam in the above suspension for 10 minutes, evaporate the solvent to dryness, and then put it into a muffle furnace protected by a hydrogen-nitrogen mixture containing 5% hydrogen by volume to react at 800°C for 10 hours, and cool naturally after the reaction is complete.
[0034] (3) Immerse the above product in 1mol / L hydrochloric acid, react at 60°C for 10h, and obtain foamed graphene after the reaction is complete.
[0035] (4) Add lithium carbonate to water, sonicate for 10 minutes to form a solution with a mass concentration of 30%, and then titrate the lithium carbonate solution onto the graphene foam, dry it, and then put it in a muffle furnace for an
Embodiment 2
[0039] (1) Add 10g of graphite oxide and 0.5g of polyacrylonitrile into a ball mill and mill for 60 minutes, then add the ball-milled mixture into a mixed solution with a volume ratio of ethanol and water of 4 and ultrasonically disperse to form a suspension with a concentration of 20g / L .
[0040] (2) Soak the nickel foam in the above suspension for 60 minutes, evaporate the solvent to dryness, and then put it into a muffle furnace protected by a hydrogen-nitrogen mixture containing 5% hydrogen by volume to react at 1100°C for 1 hour, and cool naturally after the reaction is complete.
[0041] (3) Immerse the above product in 3mol / L hydrochloric acid, react at 80°C for 5h, and obtain foamed graphene after the reaction is complete.
[0042] (4) Add lithium carbonate to water, ultrasonicate for 10-30min to form a solution with a mass concentration of 70%, then titrate the lithium carbonate solution onto the graphene foam, dry it, and then put it in a muffle furnace for 300°C a
Embodiment 3
[0046](1) Add 10g of graphite oxide and 0.1g of polyacrylonitrile into a ball mill and mill for 45 minutes, then add the ball-milled mixture into a mixed solution with a volume ratio of ethanol and water of 0.5 for ultrasonic dispersion to form a suspension with a concentration of 3g / L .
[0047] (2) Soak the nickel foam in the above suspension for 30 minutes, evaporate the solvent to dryness, and then put it into a muffle furnace protected by a hydrogen-nitrogen mixture containing 5% hydrogen by volume to react at 900°C for 5 hours, and cool naturally after the reaction is complete.
[0048] (3) Immerse the above product in 2mol / L hydrochloric acid, react at 75°C for 7h, and obtain foamed graphene after the reaction is complete.
[0049] (4) Add lithium carbonate to water, sonicate for 20 minutes to form a solution with a mass concentration of 50%, then titrate and coat the lithium carbonate solution on the foamed graphene, dry it, and then put it in a muffle furnace for ann
PUM
Property | Measurement | Unit |
---|---|---|
Thickness | aaaaa | aaaaa |
Energy density | aaaaa | aaaaa |
Abstract
Description
Claims
Application Information
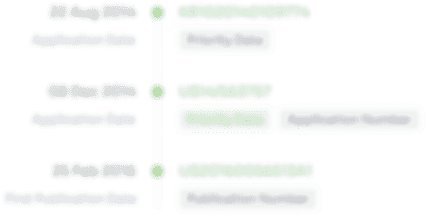
- R&D Engineer
- R&D Manager
- IP Professional
- Industry Leading Data Capabilities
- Powerful AI technology
- Patent DNA Extraction
Browse by: Latest US Patents, China's latest patents, Technical Efficacy Thesaurus, Application Domain, Technology Topic.
© 2024 PatSnap. All rights reserved.Legal|Privacy policy|Modern Slavery Act Transparency Statement|Sitemap