Nano-modified nylon material
A nano-modification, nylon technology, applied in the field of nylon materials, can solve the problems of complex operation, poor dispersion performance of nano-materials, affecting the effect of material modification, etc., and achieve the effects of excellent toughness, good application performance, and good dimensional stability.
- Summary
- Abstract
- Description
- Claims
- Application Information
AI Technical Summary
Problems solved by technology
Method used
Examples
Embodiment 1
[0012] A nano-modified nylon material described in Example 1 is composed of the following raw material components: 60 parts of polyoxymethylene, 42 parts of polyvinylidene fluoride, 45 parts of polyvinyl chloride, 60 parts of high-density polyethylene, 55 parts of polystyrene, 45 parts of polysulfone resin, 30 parts of polyphenylene ether resin, 30 parts of bismaleimide resin, 8 parts of nano aluminum powder, 5 parts of nano zirconia, 5 parts of nano copper oxide, 3 parts of nano Titanium dioxide, 5 parts of nano-zinc oxide, 4 parts of nano-aluminum nitride, 5 parts of nano-silicon powder, 4 parts of nano-silver powder, 3 parts of nano-nickel powder, 4 parts of nano-zinc powder, 8 parts of high-performance hollow glass beads, 5 parts of polymer Sodium acrylate, 6 parts methylcellulose, 45 parts deionized water.
Embodiment 2
[0014] A nano-modified nylon material described in Example 2 is composed of the following raw material components: 65 parts of polyoxymethylene, 48 parts of polyvinylidene fluoride, 50 parts of polyvinyl chloride, 65 parts of high-density polyethylene, 60 parts of polystyrene, 50 parts of polysulfone resin, 35 parts of polyphenylene ether resin, 35 parts of bismaleimide resin, 10 parts of nano aluminum powder, 8 parts of nano zirconia, 8 parts of nano copper oxide, 5 parts of nano Titanium dioxide, 6 parts of nano-zinc oxide, 5 parts of nano-aluminum nitride, 6 parts of nano-silicon powder, 5 parts of nano-silver powder, 5 parts of nano-nickel powder, 6 parts of nano-zinc powder, 10 parts of high-performance hollow glass beads, 8 parts of polymer Sodium acrylate, 8 parts methylcellulose, 50 parts deionized water.
PUM
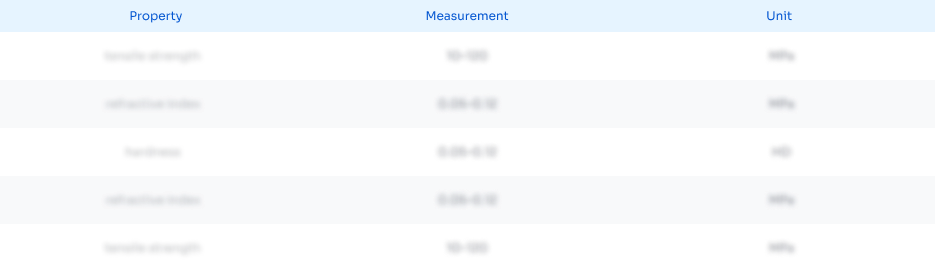
Abstract
Description
Claims
Application Information
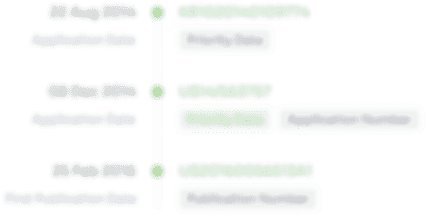
- R&D Engineer
- R&D Manager
- IP Professional
- Industry Leading Data Capabilities
- Powerful AI technology
- Patent DNA Extraction
Browse by: Latest US Patents, China's latest patents, Technical Efficacy Thesaurus, Application Domain, Technology Topic.
© 2024 PatSnap. All rights reserved.Legal|Privacy policy|Modern Slavery Act Transparency Statement|Sitemap