Magnesium steam crystallization waste heat utilization device for recycled magnesium smelting
A technology of magnesium smelting and magnesium vapor, which is applied in the field of waste heat utilization devices for magnesium vapor crystallization in recycling magnesium smelting, which can solve the problems of heat waste, large floor space, and high operating costs, and achieve water conservation, construction reduction, and improvement of utilization efficiency Effect
- Summary
- Abstract
- Description
- Claims
- Application Information
AI Technical Summary
Benefits of technology
Problems solved by technology
Method used
Image
Examples
Embodiment 1
[0011] Embodiment 1: as figure 1 As shown, the present invention includes a vertical tank 1. The upper end of the vertical tank 1 is a magnesium crystallization cylinder 4, and a closed pressure-bearing water jacket is coaxially arranged around the magnesium crystallization cylinder 4 along the circumferential direction. The inner diameter of the airtight pressure-bearing water jacket is Greater than the outer diameter of the magnesium crystallization cylinder 4, the airtight pressurized water jacket consists of a steam section 3 and a water holding section 2 from top to bottom, the steam section 3 and the water holding section 2 are connected, and at the upper end of the steam section 3 A steam outlet pipe 7 is provided, an electromagnetic gas valve 8 is installed on the steam outlet pipe 7, a water inlet pipe 10 is arranged on the upper end of the water holding section 2, and a first electromagnetic water valve 9 is installed on the water inlet pipe 10.
[0012] In the silicon
Embodiment 2
[0014] Embodiment 2: The difference from Embodiment 1 is that a water outlet pipe 12 is provided on the side wall of the water holding section 2, the water outlet pipe 12 is lower than the water inlet pipe 10, and a second electromagnetic water valve is installed on the water outlet pipe 12 13. In this way, dynamically flowing cooling water can be formed in the water storage section 2, thereby further increasing the utilization efficiency of waste heat, which is a cooling water-hot water utilization method.
PUM
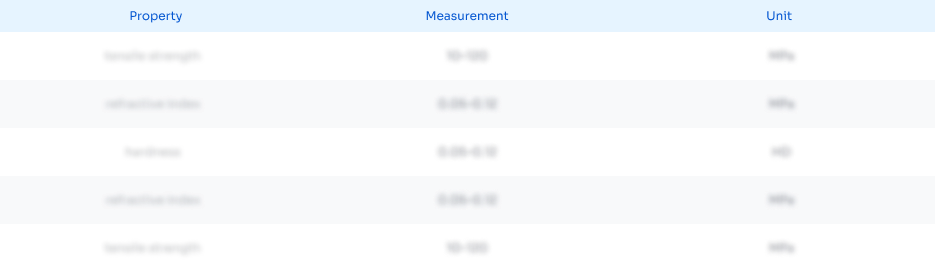
Abstract
Description
Claims
Application Information
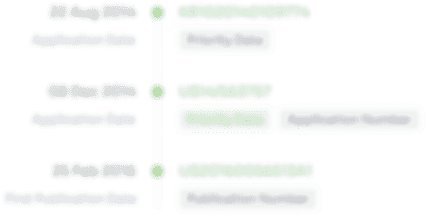
- R&D Engineer
- R&D Manager
- IP Professional
- Industry Leading Data Capabilities
- Powerful AI technology
- Patent DNA Extraction
Browse by: Latest US Patents, China's latest patents, Technical Efficacy Thesaurus, Application Domain, Technology Topic.
© 2024 PatSnap. All rights reserved.Legal|Privacy policy|Modern Slavery Act Transparency Statement|Sitemap