High-precision composite copper alloy wire and processing technology thereof
A processing technology and copper alloy technology, which is applied in the field of high-precision composite copper alloy wire and its processing technology, can solve problems such as poor quality, and achieve the effects of simple process, smooth surface and high precision
- Summary
- Abstract
- Description
- Claims
- Application Information
AI Technical Summary
Problems solved by technology
Method used
Examples
Embodiment 1
[0040] A processing technique for a high-precision composite copper alloy wire, comprising the following steps:
[0041] S1. Weigh 91 parts of copper, 2 parts of zirconium, and 8 parts of magnesium and add them to the melting furnace, and carry out melting at a temperature of 790 ° C for 36 minutes;
[0042] S2. Add 6 parts of manganese, 8 parts of iron, 16 parts of silicon, 6 parts of nickel, and 6 parts of tin into the smelting furnace, and smelt at a temperature of 790° C. for 32-45 minutes;
[0043] S3, adding 19 parts of neodymium, 15 parts of tungsten, 9 parts of carbon, 5 parts of chromium, 4 parts of lead, and 4 parts of antimony into the melting furnace, and smelting at a temperature of 890° C. for 37 minutes;
[0044] S4. Mix and stir step S1, step S2 and step S3 after smelting, then refine, and finally
[0045] Through the continuous casting machine, the copper alloy wire billet is obtained;
[0046] S5. Extruding or multi-pass drawing and annealing the copper wire b
Embodiment 2
[0049] A processing technique for a high-precision composite copper alloy wire, comprising the following steps:
[0050] S1. Weigh 93 parts of copper, 3 parts of zirconium, and 11 parts of magnesium and add them to the melting furnace, and carry out melting at a temperature of 830 ° C for 40 minutes;
[0051] S2. Add 7 parts of manganese, 14 parts of iron, 17 parts of silicon, 8 parts of nickel, and 7 parts of tin into the melting furnace, and carry out melting at a temperature of 870° C. for 45 minutes;
[0052] S3, adding 20 parts of neodymium, 17 parts of tungsten, 10 parts of carbon, 6 parts of chromium, 5 parts of lead, and 5 parts of antimony into the melting furnace, and smelting at a temperature of 930° C. for 49 minutes;
[0053] S4. Mix and stir step S1, step S2 and step S3 after smelting, then refine, and finally
[0054] Through the continuous casting machine, the copper alloy wire billet is obtained;
[0055] S5. Extruding or multi-pass drawing and annealing the co
Embodiment 3
[0060]A processing technique for a high-precision composite copper alloy wire, comprising the following steps:
[0061] S1. Weigh 89 parts of copper, 2 parts of zirconium, and 6 parts of magnesium into the melting furnace, and carry out melting at a temperature of 700 ° C for 30-40 minutes;
[0062] S2. Add 5 parts of manganese, 6 parts of iron, 12 parts of silicon, 5 parts of nickel, and 3 parts of tin into the smelting furnace, and smelt at a temperature of 750-870° C. for 32-45 minutes;
[0063] S3, adding 16 parts of neodymium, 12 parts of tungsten, 6 parts of carbon, 3 parts of chromium, 3 parts of lead, and 3 parts of antimony into the melting furnace, and smelting at a temperature of 800° C. for 31 minutes;
[0064] S4. Mix and stir step S1, step S2 and step S3 after smelting, then refine, and finally
[0065] Through the continuous casting machine, the copper alloy wire billet is obtained;
[0066] S5. Extruding or multi-pass drawing and annealing the copper wire billet
PUM
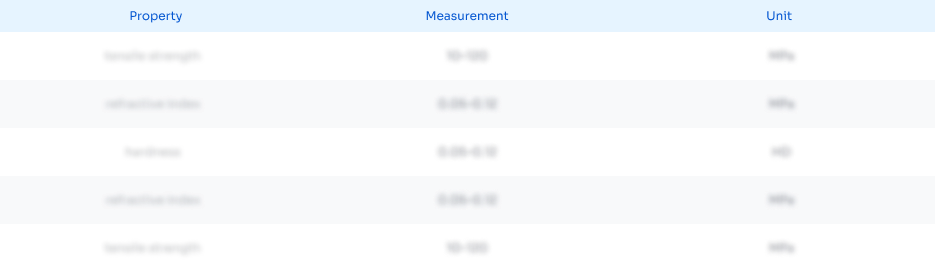
Abstract
Description
Claims
Application Information
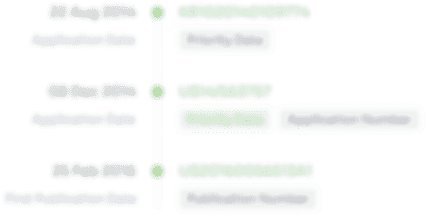
- R&D Engineer
- R&D Manager
- IP Professional
- Industry Leading Data Capabilities
- Powerful AI technology
- Patent DNA Extraction
Browse by: Latest US Patents, China's latest patents, Technical Efficacy Thesaurus, Application Domain, Technology Topic.
© 2024 PatSnap. All rights reserved.Legal|Privacy policy|Modern Slavery Act Transparency Statement|Sitemap