Method for controlling discoloration of nylon
A nylon and toner technology, applied in the nylon coloring field, can solve problems such as easy discoloration, and achieve the effects of simple operation, low price, and improved weather resistance and temperature resistance.
- Summary
- Abstract
- Description
- Claims
- Application Information
AI Technical Summary
Benefits of technology
Problems solved by technology
Method used
Image
Examples
Embodiment 1
[0028] Instrument: Minolta spectrometer 2600D
[0029] Raw materials: magnesia 100g, nylon (PA66): EPR27 100Kg, titanium dioxide: CR-69 400g, dye: Sumitomo Chemical H3G red 100g, silicone oil: Wacker AK12500 100g;
[0030] 1) Magnesium oxide and nylon were stirred for 12 minutes under the condition of 1200r / min;
[0031] 2) Add silicone oil to the material obtained in step 1) and stir for 8 minutes under the condition of 1400r / min;
[0032] 3) Stir the titanium dioxide with toner added to the material obtained in step 2) under the condition of 1150r / min for 20 minutes;
[0033] 4) Utilize twin-screw extruder to extrude and granulate.
[0034]
Embodiment 2
[0043] Instrument: Minolta spectrometer 2600D
[0044] Raw materials: magnesia 100g, nylon (PA66): EPR27 100Kg, titanium dioxide: CR-69 400g, dye: Clariant phthalocyanine blue 100g, silicone oil: Wacker AK12500 100g;
[0045] 1) Magnesium oxide and nylon were stirred for 12 minutes under the condition of 1200r / min;
[0046] 2) Add silicone oil to the material obtained in step 1) and stir for 8 minutes under the condition of 1400r / min;
[0047] 3) Stir the titanium dioxide with toner added to the material obtained in step 2) under the condition of 1150r / min for 20 minutes;
[0048] 4) Utilize twin-screw extruder to extrude and granulate.
[0049]
Embodiment 3
[0058] Instrument: Minolta spectrometer 2600D
[0059] Raw materials: magnesia 100g, nylon (PA66): EPR27 100Kg, titanium dioxide: CR-69 400g, dye: Sumitomo Chemical HFG orange 100g, silicone oil: Wacker AK12500 100g;
[0060] 1) Magnesium oxide and nylon were stirred for 12 minutes under the condition of 1200r / min;
[0061] 2) Add silicone oil to the material obtained in step 1) and stir for 8 minutes under the condition of 1400r / min;
[0062] 3) Stir the titanium dioxide with toner added to the material obtained in step 2) under the condition of 1150r / min for 20 minutes;
[0063] 4) Utilize twin-screw extruder to extrude and granulate.
[0064]
[0065]
PUM
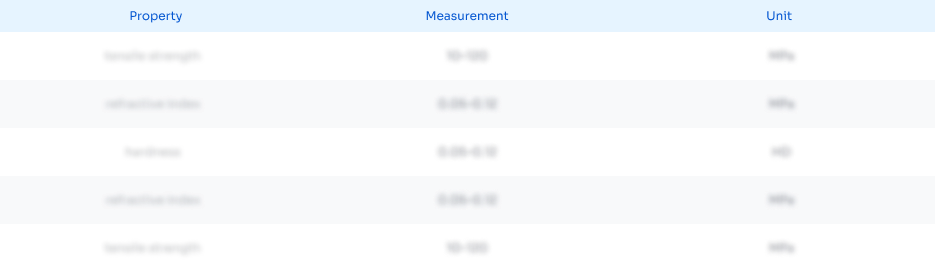
Abstract
Description
Claims
Application Information
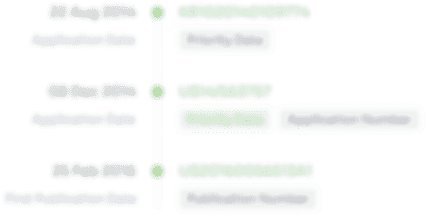
- R&D Engineer
- R&D Manager
- IP Professional
- Industry Leading Data Capabilities
- Powerful AI technology
- Patent DNA Extraction
Browse by: Latest US Patents, China's latest patents, Technical Efficacy Thesaurus, Application Domain, Technology Topic.
© 2024 PatSnap. All rights reserved.Legal|Privacy policy|Modern Slavery Act Transparency Statement|Sitemap