Ceramic material 3D printing forming method
A technology of 3D printing and molding method, applied in ceramic molding machines, additive processing, manufacturing tools, etc., can solve problems such as limiting the popularization and application of 3D printing technology, and achieve shortened development and production cycle, good uniformity, and good versatility Effect
- Summary
- Abstract
- Description
- Claims
- Application Information
AI Technical Summary
Problems solved by technology
Method used
Examples
Example Embodiment
[0032] Example 1
[0033] A computer is used to establish a three-dimensional solid model, and a layered model with a thickness of 2.0mm for each layer is generated along the z-direction to complete the scanning path program of each layer section.
[0034] Measure 100 mL of silica sol, the solid phase volume fraction is 23%; Weigh 176 g of silica powder, the particle size is 15 microns, and the purity is 98%. The above-mentioned raw materials are mixed uniformly under high-speed stirring to obtain a slurry with a solid phase volume fraction of 72%, which is added to the storage tank of the injection pump.
[0035] Set the temperature of the print work platform to -75°C, set the ejection speed of the print head to 30 mL / h, and the distance between the print head and the print platform to 1.5 mm.
[0036] Start the printing device, run the printing program, and the print head completes the printing of the first layered section according to the preset scanning path. The working platform
Example Embodiment
[0038] Example 2
[0039] Use the computer to build a three-dimensional solid model, generate a layered model with a thickness of 1.0mm for each layer along the z-direction, and complete the scanning path program of each layer section.
[0040] Weigh 88.96 grams of silicon nitride powder, the alpha phase content is 93%, the particle size is 0.40 ~ 0.60 microns; Weigh 81.98 grams of aluminum nitride powder, the particle size is 0.50 ~ 6.00 microns, the purity is 98.5%; Weigh 20 grams of silica powder with a particle size of 15 microns and a purity of 98%; weigh 11 grams of yttrium oxide powder with a particle size of 0.6 to 0.8 microns and a purity of 99.5%; measure 80 ml of silica sol, The solid content is 23%; the above powder and sol are mixed and ball milled for 30 minutes to obtain a slurry with a solid content of 57%, which is added to the storage tank of the injection pump.
[0041] Set the temperature of the print work platform to -196°C (the freezer space is filled with liquid
Example Embodiment
[0044] Example 3
[0045] Use the computer to build a three-dimensional solid model, generate a layered model with a thickness of 0.5mm for each layer along the z-direction, and complete the scanning path program of each layer section.
[0046] Measure 20 mL of aluminum sol, the solid phase volume fraction is 12%; weigh 28 g of alumina powder, the particle size is 8 microns, and the purity is 99%. The above-mentioned raw materials are mixed uniformly under high-speed stirring to obtain a slurry with a solid phase volume fraction of 35%, which is added to the storage tank of the injection pump.
[0047] Set the temperature of the print work platform to -196°C, set the ejection speed of the print head to 2 mL / h, and the distance between the print head and the print platform to 1.0 mm.
[0048] Start the printing device, run the printing program, and the print head completes the printing of the first layered section according to the preset scanning path. The working platform is lowered b
PUM
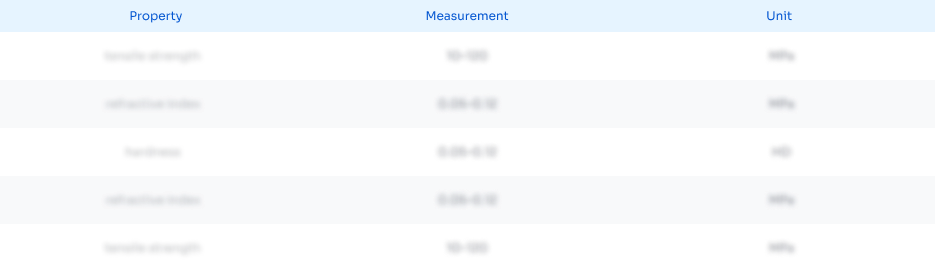
Abstract
Description
Claims
Application Information
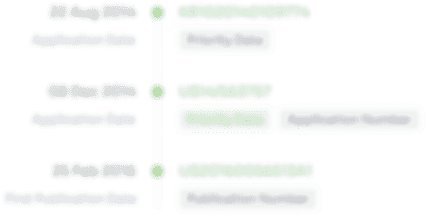
- R&D Engineer
- R&D Manager
- IP Professional
- Industry Leading Data Capabilities
- Powerful AI technology
- Patent DNA Extraction
Browse by: Latest US Patents, China's latest patents, Technical Efficacy Thesaurus, Application Domain, Technology Topic.
© 2024 PatSnap. All rights reserved.Legal|Privacy policy|Modern Slavery Act Transparency Statement|Sitemap