Chromium removal method in production and refining process of antimony smelting furnace
A refining process and reverberatory furnace technology, which is applied in the non-ferrous metal antimony smelting field, can solve problems such as restricting the application of antimony products, there is no antimony smelting reverberatory furnace chromium removal method, and affect the quality of antimony products, so as to achieve good chromium removal effect and economic benefits Remarkable, widening effect of application field
- Summary
- Abstract
- Description
- Claims
- Application Information
AI Technical Summary
Problems solved by technology
Method used
Examples
Example Embodiment
[0011] Example 1
[0012] The 18㎡ reverberatory furnace refining and chromium removal operation uses a certain alkali metal compound as a chromium removal agent. Before refining, the antimony liquid contains 0.04% chromium. The weight of the antimony liquid is estimated to be 50 tons. Add the prepared chromium removal agent 1.5 at 950℃~1000℃ Tons, the slag is discharged after 1 hour of blast stirring, and the antimony liquid contains 0.001% of chromium, which is better than the expected value, and the chromium removal effect is significant.
Example Embodiment
[0013] Example 2
[0014] 16㎡ reverberatory furnace refining chromium removal operation, using a certain alkali metal compound as a chromium removal agent. Before refining, the antimony liquid contains 0.03% chromium, and the weight of the antimony liquid is estimated to be 45 tons. Add the prepared chromium removal agent at 950℃~1000℃. Tons, the slag is discharged after 1 hour of blast agitation, and the antimony liquid contains 0.0006% of chromium, which is better than the expected value, and the chromium removal effect is significant.
PUM
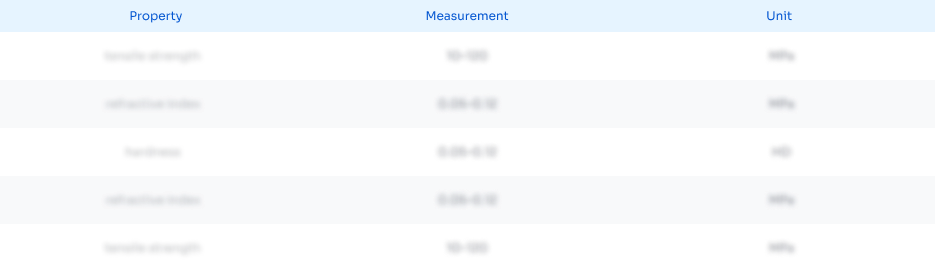
Abstract
Description
Claims
Application Information
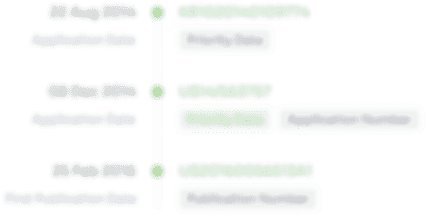
- R&D Engineer
- R&D Manager
- IP Professional
- Industry Leading Data Capabilities
- Powerful AI technology
- Patent DNA Extraction
Browse by: Latest US Patents, China's latest patents, Technical Efficacy Thesaurus, Application Domain, Technology Topic.
© 2024 PatSnap. All rights reserved.Legal|Privacy policy|Modern Slavery Act Transparency Statement|Sitemap