Track harvester hydraulic control system and control method
A hydraulic control system and technology for harvesters, which are applied to harvesters, cutters, mechanical equipment, etc., can solve the problems of unreliable steering of rice machines and the inability of multi-way valves to achieve steering priority functions, and achieve simple structure, reliable steering, Action-reliable effects
- Summary
- Abstract
- Description
- Claims
- Application Information
AI Technical Summary
Problems solved by technology
Method used
Image
Examples
Embodiment 2
[0027] Embodiment two: see Figure 4 , An electric proportional overflow valve 8 or an electric proportional throttle valve is set between the oil outlet C1 of the steering cylinder and the oil return port T. In the second embodiment, the throttle function of the steering cylinder oil outlet C1 and the control reversing valve 3 in the first embodiment is extracted separately and replaced by an electric proportional overflow valve 8 or an electric proportional throttle valve, so that the steering cylinder can Reliable oil return.
[0028]The right spring chamber 42 of the priority valve is provided with a second throttle hole 46 . The setting of the second throttle hole prevents the priority valve from being impacted during the working process of the system, making the system more stable.
[0029] A hydraulic control method for a crawler harvester, which is characterized in that it includes: ①When the control reversing valve is in the neutral position, the unloading valve is de-
PUM
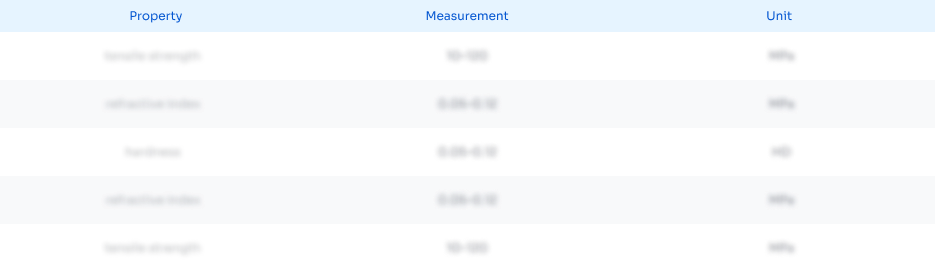
Abstract
Description
Claims
Application Information
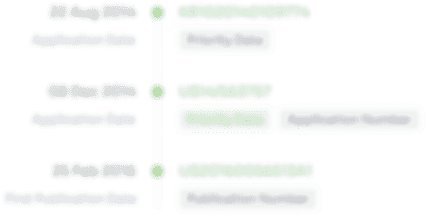
- R&D Engineer
- R&D Manager
- IP Professional
- Industry Leading Data Capabilities
- Powerful AI technology
- Patent DNA Extraction
Browse by: Latest US Patents, China's latest patents, Technical Efficacy Thesaurus, Application Domain, Technology Topic.
© 2024 PatSnap. All rights reserved.Legal|Privacy policy|Modern Slavery Act Transparency Statement|Sitemap