High-modulus carbon fiber used as thermoplastic resin-based composite reinforcement body and preparation method thereof
A thermoplastic resin and composite material technology, applied in carbon fiber, fiber treatment, physical treatment, etc., can solve problems such as lack of mechanical properties, achieve high modulus, increase functional group content, and meet processing temperature requirements
- Summary
- Abstract
- Description
- Claims
- Application Information
AI Technical Summary
Problems solved by technology
Method used
Examples
Example Embodiment
[0025] Example 1
[0026] (1) Standard carbon fiber surface purification
[0027] The surface purification of standard modulus carbon fiber is to remove the polymer material on the fiber surface by heat treatment at 400°C for 3 minutes in a nitrogen atmosphere.
[0028] (2) Ultra-high temperature graphitization
[0029] The surface-purified carbon fiber is sent to a graphitization furnace for graphitization, using nitrogen as a protective gas, and the oxygen content in the nitrogen is 1.0 ppm; the graphitization temperature is 2150° C., and the residence time is 3 minutes.
[0030] (3) Constant current electrolytic oxidation
[0031] The current density is controlled by a DC / stabilized power supply, and the high-modified carbon fiber is subjected to continuous constant current oxidation treatment in a 5% ammonium bicarbonate electrolyte solution, and the current density is 1 mA / cm 2 , The operating temperature is 50 ℃, and then rinse with deionized water to remove the residual electroly
Example Embodiment
[0035] Example 2
[0036] (1) The surface purification of standard modulus carbon fiber is the same as in Example 1.
[0037] (2) Ultra-high temperature graphitization
[0038] The surface-purified carbon fiber is fed into a graphitization furnace for high-modulation treatment, using nitrogen as a protective gas, and the oxygen content in the nitrogen is 1.0 ppm; the graphitization temperature is 2300°C, and the residence time is 3 minutes.
[0039] (3) Constant current electrolytic oxidation
[0040] The current density is controlled by a DC / stabilized power supply, the graphitized fiber is subjected to continuous constant current oxidation treatment in 5% ammonium bicarbonate electrolyte solution, and the current density is 0.8 mA / cm 2 , Operating temperature 60℃. Then rinse with deionized water to remove residual electrolyte ions on the surface and dry.
[0041] (4) Sizing agent imidization
[0042] The carbon fiber tow was fed into the aqueous polyamic acid sizing agent and immersed
Example Embodiment
[0044] Example 3
[0045] (1) The surface purification of standard carbon fiber is the same as in Example 1.
[0046] (2) Ultra-high temperature graphitization
[0047] The surface-purified carbon fiber is sent to a graphitization furnace for high-modulation treatment, using nitrogen as a protective gas, and the oxygen content in the nitrogen is 1.0 ppm; the graphitization temperature is 2500°C, and the residence time is 3 minutes.
[0048] (3) Constant current electrolytic oxidation
[0049] The current density is controlled by a DC / stabilized power supply, and the high-modified carbon fiber is subjected to continuous constant current oxidation treatment in a 5% ammonium bicarbonate electrolyte solution, and the current density is 2 mA / cm 2 , Operating temperature 40℃. Then rinse with deionized water to remove residual electrolyte ions on the surface and dry.
[0050] (4) Sizing agent imidization
[0051] The carbon fiber tow was fed into an aqueous polyamic acid sizing agent for immer
PUM
Property | Measurement | Unit |
---|---|---|
Modulus | aaaaa | aaaaa |
Interlaminar shear strength | aaaaa | aaaaa |
Tensile modulus | aaaaa | aaaaa |
Abstract
Description
Claims
Application Information
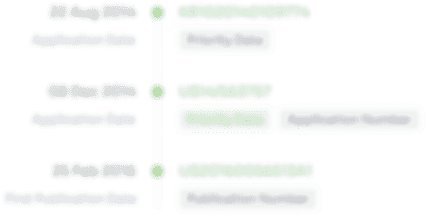
- R&D Engineer
- R&D Manager
- IP Professional
- Industry Leading Data Capabilities
- Powerful AI technology
- Patent DNA Extraction
Browse by: Latest US Patents, China's latest patents, Technical Efficacy Thesaurus, Application Domain, Technology Topic.
© 2024 PatSnap. All rights reserved.Legal|Privacy policy|Modern Slavery Act Transparency Statement|Sitemap