Method for improving power factor of cement-based composite material by pretreating zinc oxide
A composite material and power factor technology, applied in the field of materials, can solve the problems of low thermoelectric power factor, achieve high thermoelectric power factor, simple preparation process, and simple process
- Summary
- Abstract
- Description
- Claims
- Application Information
AI Technical Summary
Benefits of technology
Problems solved by technology
Method used
Image
Examples
Embodiment 1
[0025] Weigh 148.77gZnO and 1.23gAl 2 o 3 Powder, mix evenly and add 100ml of absolute ethanol, put it in a ball mill jar and mill it with a planetary ball mill for 8 hours, take it out and dry it at 60°C for 10 hours for later use. Weigh 10g of pretreated zinc oxide micropowder and spread it on the corundum board, weigh 15.6g of 400-mesh activated carbon powder and put it in a porcelain boat, place it in front of and behind the corundum board, use an air compressor to produce it, and then pass it through an air filter to purify it. Air, the gas flow rate is 30sccm, the heat treatment temperature is 1000°C, the holding time is 1 hour, and the heating rate is 5°C / min, to obtain the pretreated zinc oxide powder.
[0026] Prepare a steel mold with a cuboid cavity, weigh 5g of pretreated zinc oxide micropowder, 10g of expanded graphite and 85g of sulphoaluminate cement according to the mass ratio of 5:10:85.
[0027] Disperse the pretreated zinc oxide micropowder and expanded gra
Embodiment 2
[0032] Weigh 148.77gZnO and 1.23gAl 2 o 3 Powder, mix evenly and add 100ml of absolute ethanol, put it in a ball mill jar and mill it with a planetary ball mill for 8 hours, take it out and dry it at 60°C for 10 hours for later use. Weigh 12g of pretreated zinc oxide powder and spread it on the corundum board, weigh 20.75g of 400 mesh activated carbon powder, put it in a porcelain boat, place it in front of and behind the corundum board, use an air compressor to produce it, and then pass it through an air filter to purify it. Air, the gas flow rate is 40sccm, the heat treatment temperature is 1100°C, the holding time is 1 hour, and the heating rate is 5°C / min to obtain the pretreated zinc oxide powder.
[0033] Prepare a steel mold with a cuboid cavity, weigh 5g of pretreated zinc oxide micropowder, 10g of expanded graphite and 85g of sulphoaluminate cement according to the mass ratio of 5:10:85.
[0034] Disperse the pretreated zinc oxide micropowder and expanded graphite ev
Embodiment 3
[0037] Weigh and weigh 148.77gZnO and 1.23gAl 2 o 3 Powder, mix evenly and add 100ml of absolute ethanol, put it in a ball mill jar and mill it with a planetary ball mill for 10 hours, take it out and dry it at 60°C for 10 hours for later use. Weigh 10g of pretreated zinc oxide micropowder and spread it on the corundum board, weigh 15.6g of 400-mesh activated carbon powder and put it in a porcelain boat, place it in front of and behind the corundum board, use an air compressor to produce it, and then pass it through an air filter to purify it. Air, the gas flow rate is 30sccm, the heat treatment temperature is 900°C, the holding time is 1 hour, and the heating rate is 5°C / min, to obtain the pretreated zinc oxide powder.
[0038] Prepare a steel mold with a cuboid cavity, weigh 5g of pretreated zinc oxide micropowder, 10g of expanded graphite and 85g of sulphoaluminate cement according to the mass ratio of 5:10:85.
[0039] Disperse the pretreated zinc oxide micropowder and ex
PUM
Property | Measurement | Unit |
---|---|---|
Seebeck coefficient | aaaaa | aaaaa |
Conductivity | aaaaa | aaaaa |
Conductivity | aaaaa | aaaaa |
Abstract
Description
Claims
Application Information
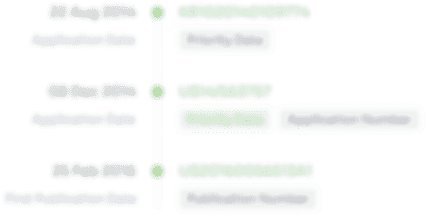
- R&D Engineer
- R&D Manager
- IP Professional
- Industry Leading Data Capabilities
- Powerful AI technology
- Patent DNA Extraction
Browse by: Latest US Patents, China's latest patents, Technical Efficacy Thesaurus, Application Domain, Technology Topic.
© 2024 PatSnap. All rights reserved.Legal|Privacy policy|Modern Slavery Act Transparency Statement|Sitemap