Production method and system of aluminum alloy coiled material/plate
A production method and production system technology, applied in the field of aluminum alloy processing, can solve the problems such as the inability of continuous heat treatment of aluminum alloy strips and low production efficiency, and achieve the effects of rapid solid solution and improved production efficiency.
- Summary
- Abstract
- Description
- Claims
- Application Information
AI Technical Summary
Benefits of technology
Problems solved by technology
Method used
Image
Examples
Embodiment 1
[0121] 1.0mm thick 2024 aluminum alloy coil production process:
[0122] S1. Coil the 1.0mm 2024 aluminum alloy coil to the uncoiler 1 after cold rolling, then the reel of the uncoiler 1 expands to the aluminum coil core, and rotates the tape head to the direction of the production line, and then passes through the uncoiler 1. The head-removing roller unrolls the tape head and sends it to the rough straightening machine 2 to complete the winding and uncoiling process of the coil;
[0123] S2. The aluminum alloy strip is passed through the rough straightening head 2, and the aluminum alloy strip is continuously bent by straightening rollers to complete the rough straightening;
[0124] Sa, make the aluminum alloy strip smoothly enter the entrance cutting head shear 3, then cut off the bad part of the strip head, and collect the waste head into the waste car;
[0125] Sb. When the tail end of the last roll of aluminum alloy strip stops at position 4 of the welding / sewing machine
Embodiment 2
[0139] 1.5mm thick 5xxx series aluminum alloy coil production process:
[0140] The process steps of this embodiment are the same as those in Implementation 1, except that step S6 is modified to: set the corresponding process speed according to the annealing and holding time requirements of the 5-series alloy, for example, 15m / min, and for a strip with a thickness of 1.5mm, set the corresponding process speed according to the annealing process It is required to choose air cooling after being out of the furnace, and choose a small air volume air cushion to control the cooling rate of the aluminum alloy strip, so as to achieve the best performance.
Embodiment 3
[0142] 2.5mm thick 6061 aluminum alloy coil production process:
[0143] The technological process step of present embodiment is identical with implementation 1, only step S6 is revised as:
[0144] At the same time, according to the solid solution time requirements of the 6-series alloy, set the corresponding process speed, for example, 3.0m / min. For the strip with a thickness of 2.5mm, according to the relationship between the strength of the 6061 alloy and the cooling rate, the curve is as follows: Figure 4 As shown, immediately enter the quenching machine after being out of the furnace, and choose the water cooling method to cool down, so as to ensure the rapid cooling of the strip after it is out of the furnace, so as to achieve the best performance, such as Figure 5 , Figure 6 As shown, the structure of the 6xxx series alloy after heat treatment is uniform, the alloy phase is fully dissolved, and the tensile strength can reach more than 230MPa.
PUM
Property | Measurement | Unit |
---|---|---|
Tensile strength | aaaaa | aaaaa |
Abstract
Description
Claims
Application Information
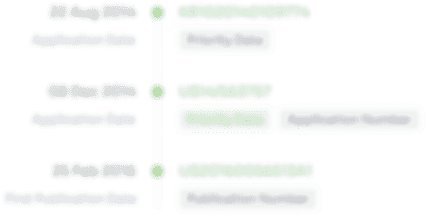
- R&D Engineer
- R&D Manager
- IP Professional
- Industry Leading Data Capabilities
- Powerful AI technology
- Patent DNA Extraction
Browse by: Latest US Patents, China's latest patents, Technical Efficacy Thesaurus, Application Domain, Technology Topic.
© 2024 PatSnap. All rights reserved.Legal|Privacy policy|Modern Slavery Act Transparency Statement|Sitemap