Chemical heat storage material and method for producing same
A chemical heat storage and manufacturing method technology, applied in chemical instruments and methods, heat exchange materials, calcium/strontium/barium oxide/hydroxide, etc., can solve the problem of reduced heat storage and heat release, poor durability, etc. problem, to achieve the effect of improving the repeated durability
- Summary
- Abstract
- Description
- Claims
- Application Information
AI Technical Summary
Benefits of technology
Problems solved by technology
Method used
Image
Examples
Embodiment
[0077] Hereinafter, specific examples according to the present invention will be described, but the present invention is not limited to the examples.
[0078]
[0079] (Preparation of surface treated calcium carbonate)
[0080] The average particle size is 20nm, the BET specific surface area is 70m 2 / g of synthetic calcium carbonate slurry (solid content concentration: 8% by mass) was heated to 40° C. while fully stirring. With respect to 100 mass parts of the synthetic calcium carbonate in this slurry, at room temperature, the sodium silicate aqueous solution is added 5 mass parts as silicon dioxide, introduces the carbon dioxide of the required amount of neutralization, thereby generates dioxane on the surface of calcium carbonate. silicon oxide layer.
[0081] Next, with respect to 100 mass parts of raw material calcium carbonate, the fatty acid mixture that was saponified by adding sodium hydroxide and heating and stirring at 90° C. was added 2 mass parts in terms of f
Embodiment 2
[0135] Operate in the same manner as in Example 1 to prepare surface-treated calcium carbonate, and decarbonate the surface-treated calcium carbonate in the same manner as in Example 1 to make the chemical heat storage material of Example 2. For the chemical heat storage material of Example 2, the hydration reaction time was set to 30 minutes, and the dehydration reaction time was set to 26.5 minutes. Under the same conditions as in Example 1, 100 repetitions were carried out. experiment.
[0136] Figure 20 For representing the maximum conversion rate (x Hy,max ) and the rate of change of the maximum conversion rate ((Δx / Δt) Hy,max ) graph. exist Figure 20 In , the left vertical axis is the maximum conversion rate x during the hydration reaction Hy,max (―), the vertical axis on the right is the change rate of the maximum conversion rate during the hydration reaction (Δx / Δt) Hy,max (S -1 ), and the horizontal axis is the cycle number of hydration reaction (-).
[013
PUM
Property | Measurement | Unit |
---|---|---|
The average particle size | aaaaa | aaaaa |
Abstract
Description
Claims
Application Information
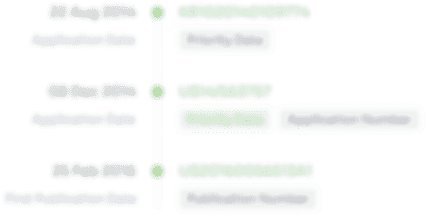
- R&D Engineer
- R&D Manager
- IP Professional
- Industry Leading Data Capabilities
- Powerful AI technology
- Patent DNA Extraction
Browse by: Latest US Patents, China's latest patents, Technical Efficacy Thesaurus, Application Domain, Technology Topic.
© 2024 PatSnap. All rights reserved.Legal|Privacy policy|Modern Slavery Act Transparency Statement|Sitemap