Heat-insulating and cooling polymer master batch, polymer material and preparation method thereof
A polymer material and polymer technology, applied in the field of polymer materials and their preparation, heat insulation and cooling polymer masterbatch, can solve the problem of low solar spectrum reflectivity, heat insulation and cooling are linked together, and chromium oxide reflectivity is not high. higher question
- Summary
- Abstract
- Description
- Claims
- Application Information
AI Technical Summary
Benefits of technology
Problems solved by technology
Method used
Image
Examples
Embodiment 1
[0048]Ingredients formula (mass ratio, parts)
[0049]Polymer masterbatch formula: HDPE (load 2160g, MFR = 18g / 10min at 190℃) 56, Cr2O3(The particle size is 0.5μm, the purity is 99.9%, the thermal weight loss rate at 600°C is 0.05%) 40, antioxidant 300 1.0, polyethylene wax 1.0, erucamide 1.0, zinc stearate 1.0.
[0050]Polymer material formula: HDPE (load 2160g, MFR=2.0g / 10min at 190℃) 97.5, polymer masterbatch (Cr2O3The content is 40wt%, the load is 2160g, and the temperature is 190°C, MFR=3.0g / 10min) 2.5.
[0051]Preparation Process:
[0052]Additive dilution and high-speed mixing: In a high-speed mixer, 6 parts of HDPE powder resin antioxidant 300, polyethylene wax, zinc stearate and 1 part of erucamide in the formula raw materials are rotated at a low speed (below 500rpm) ) Stir for 4 minutes, start high-speed stirring (above 1000 rpm) for 2 minutes, and then discharge to another mixer with jacket water cooling. When the temperature drops to 40℃, discharge to the dilution aid silo;
[0053
Embodiment 2
[0056]Ingredients formula (mass ratio, parts)
[0057]Polymer masterbatch formula: HDPE (load 2160g, MFR = 20g / 10min at 190℃) 46, Cr2O3(The particle size is 1.0μm, the purity is 99.8%, the thermal weight loss rate at 600°C is 0.1%) 50, antioxidant 300 1.0, polyethylene wax 1.0, erucamide 1.0, zinc stearate 1.0.
[0058]Polymer material formula: HDPE (load 2160g, MFR = 1.5g / 10min at 190℃) 98.0, polymer masterbatch (Cr2O3The content is 50wt%, the load is 2160g, and the temperature is 190°C, MFR=2.0g / 10min)2.0.
[0059]Preparation Process:
[0060]Additive dilution and high-speed mixing: In a high-speed mixer, 6 parts of HDPE powder resin antioxidant 300, polyethylene wax, zinc stearate and 1 part of erucamide in the formula raw materials are rotated at a low speed (below 500rpm) ) Stir for 3 minutes, start high-speed stirring (above 1000 rpm) for 2 minutes and then discharge to another mixer with jacket water cooling. When the temperature drops to 35°C, discharge to the dilution aid silo;
[0061
Embodiment 3
[0064]Raw material formula (mass ratio, parts):
[0065]Polymer masterbatch formula: HDPE (load 2160g, MFR = 20g / 10min at 190℃) 51, Cr2O3(The particle size is 1.0μm, the purity is 99.9%, the thermal weight loss rate at 600°C is 0.1%) 45, antioxidant 300 1.0, polyethylene wax 1.0, erucamide 1.0, zinc stearate 1.0.
[0066]Polymer material formula: LDPE (load 2160g, MFR = 0.5g / 10min at 190℃) 93.3, polymer masterbatch (Cr2O3The content is 45wt%, the load is 2160g, and the temperature is 190°C, MFR=1.0g / 10min)6.7.
[0067]Preparation Process:
[0068]Additive dilution and high-speed mixing: In a high-speed mixer, 6 parts of HDPE powder resin antioxidant 300, polyethylene wax, zinc stearate and 1 part of erucamide in the formula raw materials are rotated at a low speed (below 500rpm) ) Stir for 2min, start high-speed stirring (above 1000rpm) for 3min, then discharge to another mixer with jacket water cooling, when the temperature drops to 45℃, discharge to the dilution aid silo;
[0069]Polymer mast
PUM
Property | Measurement | Unit |
---|---|---|
Particle size | aaaaa | aaaaa |
Particle size | aaaaa | aaaaa |
Abstract
Description
Claims
Application Information
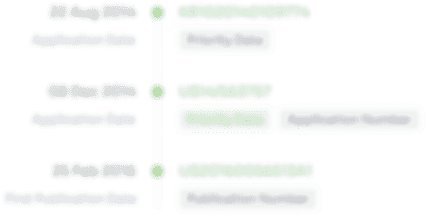
- R&D Engineer
- R&D Manager
- IP Professional
- Industry Leading Data Capabilities
- Powerful AI technology
- Patent DNA Extraction
Browse by: Latest US Patents, China's latest patents, Technical Efficacy Thesaurus, Application Domain, Technology Topic.
© 2024 PatSnap. All rights reserved.Legal|Privacy policy|Modern Slavery Act Transparency Statement|Sitemap