Rod-needle separated magnesium alloy slim tube preparation device and method
A preparation device and magnesium alloy technology, applied in the direction of metal extrusion dies, metal extrusion mandrels, etc., can solve the problems of difficult to ensure the dimensional accuracy of pipes, reduce the strength of pipes, and reduce stability, so as to achieve good surface quality and reduce processing costs. High cost and compactness
- Summary
- Abstract
- Description
- Claims
- Application Information
AI Technical Summary
Benefits of technology
Problems solved by technology
Method used
Image
Examples
Embodiment example 1
[0039] This implementation case relates to a method for preparing a thin magnesium alloy tube separated from a rod and a needle, and the method includes the following steps:
[0040] (1) Carry out wire-cutting, turning processing, and drilling of Mg-1.84Zn-0.31Mn-0.18Ca alloy ingot to obtain a hollow cylindrical billet with an outer diameter of 30 mm, a height of 15 mm, and a middle through hole diameter of 6.5 mm;
[0041] (2) Apply graphite-based lubricant to the inner wall of the extrusion cylinder, the wall of the extrusion die hole, the surface of the extrusion needle, and the lower surface of the extrusion needle cushion, and then put it in a resistance furnace and heat it to 400 ° C, put in a hollow cylindrical blank, and keep warm 5min;
[0042] (3) Take out the mold and the billet, assemble them on the extrusion die base, install them, and carry out extrusion when the temperature drops to 380°C. The extrusion ratio is 30.6:1, and the extrusion speed is 2mm / s to obtain
Embodiment example 2
[0046] This implementation case relates to a method for preparing a thin magnesium alloy tube separated from a rod and a needle, and the method includes the following steps:
[0047] (1) Carry out wire-cutting, turning processing, and drilling of Mg-1.85Zn-0.21Mn-0.21Ca alloy ingot to obtain a hollow cylindrical billet with an outer diameter of 30 mm, a height of 15 mm, and a middle through hole diameter of 6.5 mm;
[0048] (2) Apply graphite-based lubricant to the inner wall of the extrusion cylinder, the wall of the extrusion die hole, the surface of the extrusion needle, and the lower surface of the extrusion needle cushion, and then put it in a resistance furnace and heat it to 400 ° C, put in a hollow cylindrical blank, and keep warm 5min;
[0049] (3) Take out the mold and the billet, assemble them on the extrusion die base, install them, and carry out extrusion when the temperature drops to 360°C. The extrusion ratio is 13.4:1, and the extrusion speed is 3mm / s to obtain
Embodiment example 3
[0053] This implementation case relates to a method for preparing a thin magnesium alloy tube separated from a rod and a needle, and the method includes the following steps:
[0054] (1) Carry out wire-cutting, turning processing, and drilling of the Mg-4.11Zn-0.26Mn-0.16Ca alloy ingot to obtain a hollow cylindrical blank with an outer diameter of 30 mm, a height of 15 mm, and a middle through hole diameter of 6.5 mm;
[0055] (2) Apply graphite-based lubricant to the inner wall of the extrusion cylinder, the hole wall of the extrusion die, the surface of the extrusion needle, and the lower surface of the extrusion needle cushion, and then put it in a resistance furnace and heat it to 420°C, put a hollow cylindrical blank, and keep warm 5min;
[0056] (3) Take out the mold and the billet, assemble them on the extrusion die base, install them, and carry out extrusion when the temperature drops to 390°C. The extrusion ratio is 30.6:1, and the extrusion speed is 3mm / s to obtain se
PUM
Property | Measurement | Unit |
---|---|---|
Section diameter | aaaaa | aaaaa |
Wall thickness | aaaaa | aaaaa |
Tensile strength | aaaaa | aaaaa |
Abstract
Description
Claims
Application Information
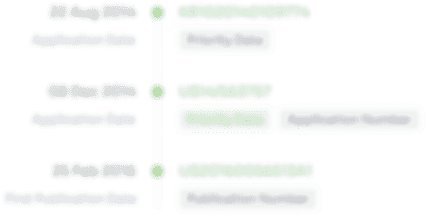
- R&D Engineer
- R&D Manager
- IP Professional
- Industry Leading Data Capabilities
- Powerful AI technology
- Patent DNA Extraction
Browse by: Latest US Patents, China's latest patents, Technical Efficacy Thesaurus, Application Domain, Technology Topic.
© 2024 PatSnap. All rights reserved.Legal|Privacy policy|Modern Slavery Act Transparency Statement|Sitemap