Preparation method of high-quality tungsten-titanium sputtering target material
A sputtering target, high-quality technology, applied in sputtering coating, metal material coating process, vacuum evaporation coating and other directions, can solve the problem of low purity of tungsten titanium target, uneven microstructure, poor thickness uniformity, etc. problems, to facilitate industrial mass production, meet the needs of high-end targets, and achieve the effect of high density
- Summary
- Abstract
- Description
- Claims
- Application Information
AI Technical Summary
Benefits of technology
Problems solved by technology
Method used
Image
Examples
preparation example Construction
[0035] A method for preparing a high-quality tungsten-titanium sputtering target, comprising the steps of:
[0036] 1.) Select tungsten powder and titanium powder, and mix them according to their mass ratio to obtain tungsten-titanium mixed powder; in this step, the purity of tungsten powder is preferably ≥99.95%, and the purity of titanium powder is preferably ≥99.95%, and the mixture is mixed to obtain tungsten In the titanium mixed powder, according to the mass percentage, the titanium powder is 8%~12%, and the rest is tungsten powder. And it is preferred that the tungsten powder and titanium powder pass through a 200-mesh sieve before the proportioning and mixing. Tungsten powder and titanium powder can be mixed in a V-shaped mixer in an argon atmosphere, and the mixing time is preferably 10~16h.
[0037] 2) Put the tungsten-titanium mixed powder obtained in step 1) into the rubber sleeve mold, after sealing the rubber sleeve mold, take a solid shot of the mold to ensure tha
Embodiment 1
[0061] 1.) Select tungsten powder and titanium powder, and mix them according to their mass ratio to obtain tungsten-titanium mixed powder: select tungsten powder and titanium powder with a purity ≥ 99.95%, and sieve them (usually use a 200-mesh sieve), sieve In addition to agglomerated particles, it is convenient for the tungsten powder and titanium powder to be fully mixed. Then mix tungsten powder and titanium powder according to the mass percentage of 90% tungsten powder and 10% titanium powder, and put the mixed powder into V-type mixer for mixing. Before starting the V-type mixer, argon protection was introduced to ensure that the argon pressure in the V-type mixer was positive. The powder mixing time in this embodiment was 14 hours.
[0062] 2) Put the tungsten-titanium mixed powder obtained in step 1) into the rubber sleeve mold, such as figure 1 shown. In this embodiment, the rubber sleeve mold 1 is cylindrical, and the upper end of the rubber sleeve mold 1 has a powde
Embodiment 2
[0075] 1.) Select tungsten powder and titanium powder, and mix them according to their mass ratio to obtain tungsten-titanium mixed powder: select tungsten powder and titanium powder with a purity ≥ 99.95%, and sieve them (usually use a 200-mesh sieve), sieve In addition to agglomerated particles, it is convenient for the tungsten powder and titanium powder to be fully mixed. Then, according to the mass percentage of tungsten powder 88% and titanium powder 12%, the tungsten powder and titanium powder are mixed, and the mixed powder after mixing is put into a V-shaped mixer for mixing. Before starting the V-type mixer, argon protection is introduced to ensure that the argon pressure in the V-type mixer is positive. The powder mixing time of this embodiment is 10 hours.
[0076] 2) Put the tungsten-titanium mixed powder obtained in step 1) into the rubber sleeve mold, such as figure 1 shown. In this embodiment, the rubber sleeve mold 1 is cylindrical, and the upper end of the rub
PUM
Property | Measurement | Unit |
---|---|---|
Roughness | aaaaa | aaaaa |
Density | aaaaa | aaaaa |
Density | aaaaa | aaaaa |
Abstract
Description
Claims
Application Information
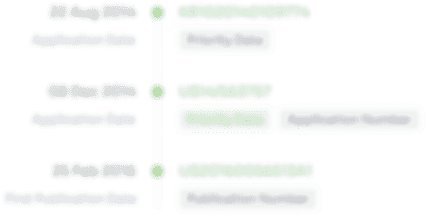
- R&D Engineer
- R&D Manager
- IP Professional
- Industry Leading Data Capabilities
- Powerful AI technology
- Patent DNA Extraction
Browse by: Latest US Patents, China's latest patents, Technical Efficacy Thesaurus, Application Domain, Technology Topic.
© 2024 PatSnap. All rights reserved.Legal|Privacy policy|Modern Slavery Act Transparency Statement|Sitemap