Heat-insulating glass glaze and preparation method thereof
A technology for insulating glass and glaze, applied in the field of insulating glass glaze and its preparation, can solve the problem of high glass transition temperature of glass powder and achieve the effect of improving the transmittance of visible light
- Summary
- Abstract
- Description
- Claims
- Application Information
AI Technical Summary
Benefits of technology
Problems solved by technology
Method used
Examples
Embodiment 1
[0028] A method for preparing a heat-insulating glass frit, comprising uniformly mixing low-melting-point glass powder, a heat radiation blocker, sodium silicate and a heat-conducting blocker to obtain a heat-insulating glass frit; The ratio of powder, heat conduction blocker, sodium silicate and heat radiation blocker is 70:5:1:5, heat radiation blocker is ATO (antimony doped tin oxide) nano powder, heat conduction blocker is nano silicon dioxide airgel.
[0029] The preparation method of low melting point glass powder, comprises the following steps:
[0030] 1) Mix the raw materials evenly, and melt at 600°C for 30 minutes to obtain molten glass, wherein the raw materials include: 25 parts by mass of SnCl 2 , 10 parts by mass of P 2 o 5 , 10 mass parts of B 2 o 3 , 0.5 parts by mass of Li 2 O, 2 parts by mass of ZrO 2 , 3 parts by mass of Na 2 O, 1 mass part of NaF, 10 mass parts of Bi 2 o 3 ;
[0031] 2) Quenching the molten glass: Pour the molten glass into a coppe
Embodiment 2
[0034] A method for preparing a heat-insulating glass frit, comprising uniformly mixing low-melting-point glass powder, a heat radiation blocker, sodium silicate and a heat-conducting blocker to obtain a heat-insulating glass frit; The ratio of powder, heat conduction blocker, sodium silicate and heat radiation blocker is 70:5:2:5, heat radiation blocker is ATO (antimony doped tin oxide) nano powder, heat conduction blocker is nano silicon dioxide airgel.
[0035] The preparation method of low melting point glass powder, comprises the following steps:
[0036] 1) Mix the raw materials evenly, and melt at 600°C for 30 minutes to obtain molten glass, wherein the raw materials include: 25 parts by mass of SnCl 2 , 10 parts by mass of P 2 o 5 , 10 mass parts of B 2 o 3 , 0.5 parts by mass of Li 2 O, 2 parts by mass of ZrO 2 , 3 parts by mass of Na 2 O, 1 mass part of NaF, 10 mass parts of Bi 2 o 3 ;
[0037] 2) Quenching the molten glass: Pour the molten glass into a coppe
Embodiment 3
[0040] A method for preparing a heat-insulating glass frit, comprising uniformly mixing low-melting-point glass powder, a heat radiation blocker, sodium silicate and a heat-conducting blocker to obtain a heat-insulating glass frit; The ratio of powder, heat conduction blocker, sodium silicate and heat radiation blocker is 70:5:3:5, heat radiation blocker is ATO (antimony doped tin oxide) nano powder, heat conduction blocker is nano silicon dioxide airgel.
[0041] The preparation method of low melting point glass powder, comprises the following steps:
[0042] 1) Mix the raw materials evenly, and melt at 600°C for 30 minutes to obtain molten glass, wherein the raw materials include: 25 parts by mass of SnCl 2 , 10 parts by mass of P 2 o 5 , 10 mass parts of B 2 o 3 , 0.5 parts by mass of Li 2O, 2 parts by mass of ZrO 2 , 3 parts by mass of Na 2 O, 1 mass part of NaF, 10 mass parts of Bi 2 o 3 ;
[0043] 2) Quenching the molten glass: Pour the molten glass into a copper
PUM
Property | Measurement | Unit |
---|---|---|
Particle size | aaaaa | aaaaa |
Thickness | aaaaa | aaaaa |
Glass transition temperature | aaaaa | aaaaa |
Abstract
Description
Claims
Application Information
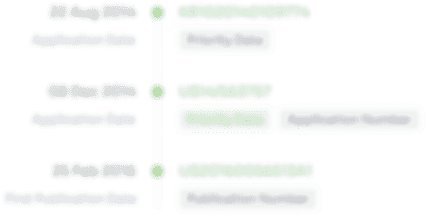
- R&D Engineer
- R&D Manager
- IP Professional
- Industry Leading Data Capabilities
- Powerful AI technology
- Patent DNA Extraction
Browse by: Latest US Patents, China's latest patents, Technical Efficacy Thesaurus, Application Domain, Technology Topic.
© 2024 PatSnap. All rights reserved.Legal|Privacy policy|Modern Slavery Act Transparency Statement|Sitemap