Short-process non-consumable arc melting preparation method of high-density high-melting-point tungsten alloy
An arc melting and arc melting furnace technology, applied in the field of short-flow non-consumable arc melting preparation, can solve problems such as long production cycle, and achieve the effects of reducing preparation cost, high processing efficiency and strong reproducibility
- Summary
- Abstract
- Description
- Claims
- Application Information
AI Technical Summary
Benefits of technology
Problems solved by technology
Method used
Image
Examples
Embodiment Construction
[0029] The invention designs and uses the non-consumable arc smelting method, and rapidly prepares high-density and high-melting tungsten alloys on the basis of optimizing the powder pressing process. Higher concentration, part of the original impurities in the sample or the trace impurities introduced and generated during the preparation process will be purified at high temperature, which has a certain purification effect. The main process flow is as follows: First, uniformly mix the alloy powder in a 3D mixer, and then use cold isostatic pressing to obtain a block-shaped green body. Under the condition of ensuring the vacuum degree (≤4Pa) in the furnace, argon gas is introduced. , using the non-consumable arc melting method to preheat, premelt, smelt and remelt the sample (4-6 times), and obtain a high-density tungsten alloy with high melting point (above 97.5%) after rapid cooling.
PUM
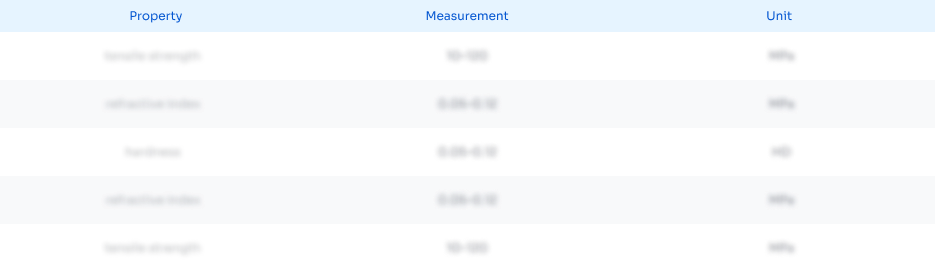
Abstract
Description
Claims
Application Information
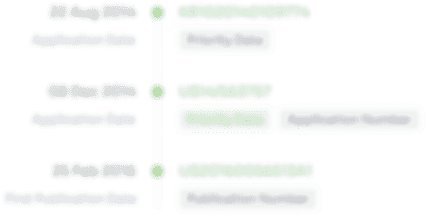
- R&D Engineer
- R&D Manager
- IP Professional
- Industry Leading Data Capabilities
- Powerful AI technology
- Patent DNA Extraction
Browse by: Latest US Patents, China's latest patents, Technical Efficacy Thesaurus, Application Domain, Technology Topic.
© 2024 PatSnap. All rights reserved.Legal|Privacy policy|Modern Slavery Act Transparency Statement|Sitemap