Low-thermal-shrinkage lithium ion battery diaphragm and preparation method thereof
A lithium-ion battery and separator technology, applied in the field of low-heat-shrinkable lithium-ion battery separator and its preparation, can solve problems such as narrowing of width, short circuit of positive and negative electrodes, and violent tendons of winding, so as to prevent winding wrinkles and reduce heat shrinkage rate, reduce the effect of heat shrinkage
- Summary
- Abstract
- Description
- Claims
- Application Information
AI Technical Summary
Problems solved by technology
Method used
Image
Examples
Embodiment 1
[0031] S1: Mixing: Stir and mix other raw materials except white oil evenly to form a mixture;
[0032] S2: Melt extrusion: mix the mixture and white oil evenly, melt, set the screw speed to 35rmp, the extrusion temperature to 200°C, the casting temperature to 22°C, and extrude to form a sheet;
[0033] S3: Longitudinal stretching: set the process parameters of longitudinal stretching as follows: the stretching temperature is 105°C, the stretching ratio is 7.5, and the sheet is stretched longitudinally to obtain film A;
[0034] S4: One-time transverse stretching: set the process parameters of one-time transverse stretching as follows: stretching temperature is 120°C, stretching ratio is 8.7, stretching retraction ratio is 12, "stretching zone - no stretching zone - retraction The length ratio of the area" is 1:1:1, and the film A is stretched transversely once to obtain the film B;
[0035] S5: extraction: extracting the film B in a solvent to obtain a film C;
[0036] S6: Sec
Embodiment 2
[0040] S1: Mixing: Stir and mix other raw materials except white oil evenly to form a mixture;
[0041]S2: Melt extrusion: mix the mixture and white oil evenly, melt, set the screw speed to 35rmp, the extrusion temperature to 200°C, the casting temperature to 22°C, and extrude to form a sheet;
[0042] S3: Longitudinal stretching: set the process parameters of longitudinal stretching as follows: the stretching temperature is 105°C, the stretching ratio is 7.5, and the sheet is stretched longitudinally to obtain film A;
[0043] S4: One-time transverse stretching: set the process parameters of one-time transverse stretching as follows: stretching temperature is 120°C, stretching ratio is 8.5, stretching retraction ratio is 12, "stretching zone-no stretching zone-retraction The length ratio of the area" is 1:1:1, and the film A is stretched transversely once to obtain the film B;
[0044] S5: extraction: extracting the film B in a solvent to obtain a film C;
[0045] S6: Secondar
Embodiment 3
[0049] S1: Mixing: Stir and mix other raw materials except white oil evenly to form a mixture;
[0050] S2: Melt extrusion: mix the mixture and white oil evenly, melt, set the screw speed to 35rmp, the extrusion temperature to 200°C, the casting temperature to 22°C, and extrude to form a sheet;
[0051] S3: Longitudinal stretching: set the process parameters of longitudinal stretching as follows: the stretching temperature is 105°C, the stretching ratio is 7.5, and the sheet is stretched longitudinally to obtain film A;
[0052] S4: One-time transverse stretching: set the process parameters of one-time transverse stretching as follows: stretching temperature is 120°C, stretching ratio is 8.6, stretching retraction ratio is 12, "stretching zone - no stretching zone - retraction The length ratio of the area" is 1:1:1, and the film A is stretched transversely once to obtain the film B;
[0053] S5: extraction: extracting the film B in a solvent to obtain a film C;
[0054] S6: Sec
PUM
Property | Measurement | Unit |
---|---|---|
Air permeability | aaaaa | aaaaa |
Abstract
Description
Claims
Application Information
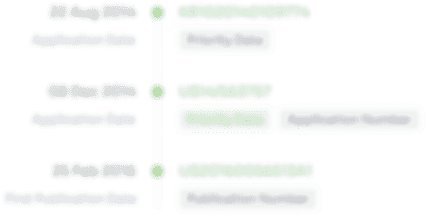
- R&D Engineer
- R&D Manager
- IP Professional
- Industry Leading Data Capabilities
- Powerful AI technology
- Patent DNA Extraction
Browse by: Latest US Patents, China's latest patents, Technical Efficacy Thesaurus, Application Domain, Technology Topic.
© 2024 PatSnap. All rights reserved.Legal|Privacy policy|Modern Slavery Act Transparency Statement|Sitemap