Ceramic digital protective glaze ink as well as preparation method and application thereof
A glaze protection, digital technology, applied in applications, inks, household appliances, etc., can solve the problems of unfavorable development, fierce price war, serious product homogeneity, etc.
- Summary
- Abstract
- Description
- Claims
- Application Information
AI Technical Summary
Benefits of technology
Problems solved by technology
Method used
Image
Examples
preparation example Construction
[0062] In some embodiments, the preparation method includes the steps of:
[0063] Step A: preparing powder;
[0064] Step B: Mix the solvent, hyperdispersant, powder, surfactant and anti-sedimentation agent, and then grind until the fineness is D50<400nm to obtain a slurry;
[0065] Step C: filter the slurry, and pack to obtain the finished ceramic digital protective glaze ink.
[0066] In some embodiments, the step A includes:
[0067] Mix the powder raw materials;
[0068] The mixed powder raw materials are refined.
[0069] In some embodiments, coulter mixer or wet ball mill mixing is used.
[0070] In some embodiments, jet mill or wet sand mill is used to refine the powder raw material, and the refinement treatment requires a particle size D100<15 μm, and further requires a particle size D100<10 μm.
[0071] In some embodiments, in step B, a sand mill is used for grinding.
[0072] In some embodiments, the mill is a horizontal sand mill.
[0073] In some embodiments,
Embodiment 1
[0089] The digital protective glaze ink is prepared according to the following formula, and the digital protective glaze matte I ink is composed of the following components according to the mass percentage:
[0090] Powder 45%
[0091] Lamberti 1087 3%
[0092] Lubrizol Solsperse 13940 3%
[0093] TOTAL PW 25-28H 48.5%
[0094] TWEEN30 0.1%
[0095] Lubrizol IRCOGEL900 0.4%
[0096] The chemical composition of the powder is calculated in parts by weight of oxides, including: Na 2 O: 5 parts, Al 2 o 3 : 23 parts, SiO 2 : 50 parts, ZnO: 4.5 parts, CaO: 16.5 parts and MgO: 1 part.
[0097] The preparation method of described preparation digital protective glaze ink comprises the following steps:
[0098] Preparation of powder: use a coulter mixer to mix the powder raw materials; use a jet mill or refine the mixed powder raw materials to a particle size of D100<10 μm.
[0099] Mix TOTAL PW 25-28H, Lamberti 1028, Lubrizol Solsperse 13940, TWEEN30 and Lubrizol IRCOGEL900 even
Embodiment 2
[0103] The digital protective glaze ink is prepared according to the following formula, and the digital protective glaze matte I ink is composed of the following components according to the mass percentage:
[0104] Powder 44%
[0105] Lamberti 1028 3%
[0106] Lubrizol Solsperse 13940 3%
[0107] TOTAL PW 25-28H 49.5%
[0108] TWEEN30 0.1%
[0109] Lubrizol IRCOGEL900 0.4%
[0110] The chemical composition of the powder is calculated in parts by weight of oxides, including: Na 2 O: 5 parts, Al 2 o 3 : 23 parts, SiO 2 : 50 parts, ZnO: 4.5 parts, CaO: 16.5 parts and MgO: 1 part.
[0111] The preparation method of described preparation digital protective glaze ink comprises the following steps:
[0112] Preparation of powder: use a coulter mixer to mix the powder raw materials; use a jet mill or refine the mixed powder raw materials to a particle size of D100<10 μm.
[0113]Mix Lamberti 1028, Lubrizol Solsperse 13940, TOTAL PW 25-28H, TWEEN30 and Lubrizol IRCOGEL900 evenl
PUM
Property | Measurement | Unit |
---|---|---|
Viscosity | aaaaa | aaaaa |
Surface tension | aaaaa | aaaaa |
Abstract
Description
Claims
Application Information
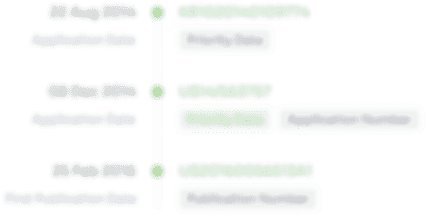
- R&D Engineer
- R&D Manager
- IP Professional
- Industry Leading Data Capabilities
- Powerful AI technology
- Patent DNA Extraction
Browse by: Latest US Patents, China's latest patents, Technical Efficacy Thesaurus, Application Domain, Technology Topic.
© 2024 PatSnap. All rights reserved.Legal|Privacy policy|Modern Slavery Act Transparency Statement|Sitemap