Preparation method of dew-point-resistant protection coating for automobile oxygen sensor
A technology for a vehicle oxygen sensor and a protective coating is applied in the field of preparation of an anti-dew point protective coating for a vehicle oxygen sensor, which can solve problems such as failure of the oxygen sensor, micro-cracks, etc., and achieves simple preparation method, simple production control, and working temperature. wide range of effects
- Summary
- Abstract
- Description
- Claims
- Application Information
AI Technical Summary
Benefits of technology
Problems solved by technology
Method used
Image
Examples
preparation example Construction
[0024] A preparation method for an anti-dew point protective coating of an oxygen sensor for a vehicle, characterized in that it comprises the following steps:
[0025] A. Prepare raw materials: Prepare micron-sized ceramic particles, metal micropowder, glass micropowder and pore-forming agent as solid particle materials; prepare dispersant, binder and absolute ethanol solvent as additives;
[0026] B. Preparation of slurry: Mix micron-sized ceramic particles, metal micropowder, glass micropowder, dispersant, binder and absolute ethanol solvent through a ball mill, and configure it to have a stable viscosity range of 515-1313mpa.s slurry;
[0027] C. Pore-making: add a pore-forming agent to the slurry, and use a stirring and defoaming mixer to mix the slurry;
[0028] D. Coating: apply the slurry obtained in step C to the surface of the oxygen sensor substrate by spin coating, spray coating or dipping;
[0029] E. Degreasing: place the coated green body in the degreasing furnac
Embodiment 1
[0044] The coating material is composed of ceramic particles. During the preparation process, the alumina particles are mixed with a pore-forming agent, and the powder is dispersed by ball milling. The pore-forming agent accounts for 15-30 wt.% of the ceramic particles. The composite powder and Organic additives such as dispersant, binder and solvent are mixed to obtain alumina coating slurry, in which the mass fraction of ceramic particles reaches 60-80 wt.%, and the slurry is coated on the sensor by dipping and pulling method The surface of the ceramic substrate is degreased and sintered to obtain a porous alumina ceramic coating with a suitable thickness and porosity, wherein the coating thickness is between 0.3 mm and 0.8 mm.
Embodiment 2
[0046] The coating material is composed of ceramic particles, glass micropowder, and an appropriate amount of pore-forming agent, in which glass micropowder accounts for 5-10 wt.% of the mass fraction of ceramic particles, and 20-40 wt.% of pore-forming agent ceramic particles. The coating design Thickness 0.2mm to 0.6mm. The softening temperature of the glass is about 700 ℃. The molten glass powder at high temperature can strengthen the bonding force between the alumina ceramic particles and between the coating and the substrate, which significantly improves the porosity of the ceramic coating without affecting the porosity of the ceramic coating. Coating resistance to thermal shock.
PUM
Property | Measurement | Unit |
---|---|---|
Diameter | aaaaa | aaaaa |
Particle size | aaaaa | aaaaa |
Thickness | aaaaa | aaaaa |
Abstract
Description
Claims
Application Information
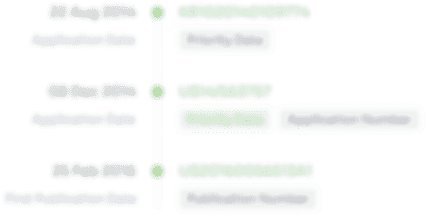
- R&D Engineer
- R&D Manager
- IP Professional
- Industry Leading Data Capabilities
- Powerful AI technology
- Patent DNA Extraction
Browse by: Latest US Patents, China's latest patents, Technical Efficacy Thesaurus, Application Domain, Technology Topic.
© 2024 PatSnap. All rights reserved.Legal|Privacy policy|Modern Slavery Act Transparency Statement|Sitemap