Ceramic glaze and preparation method thereof
一种陶瓷釉料、原料的技术,应用在陶瓷领域,能够解决瓷釉化学稳定性不高、耐磨性不高、颜色不均匀等问题,达到良好上色效果、增加耐磨性能、不易团聚的效果
- Summary
- Abstract
- Description
- Claims
- Application Information
AI Technical Summary
Problems solved by technology
Method used
Examples
Embodiment 1
[0034] A ceramic glaze made of the following raw materials by weight: 35 parts of nano-silica, 55 parts of kaolin, 15 parts of albite, 5 parts of magnesium oxide, 5 parts of sodium oxide, 25 parts of dolomite, 25 parts of limestone, 3 parts of pigments and fillers, 15 parts of modified additives, 55 parts of deionized water;
[0035] The ceramic glaze is made by the following method:
[0036] Step S1. Activation of kaolin: (a) Put the kaolin in a muffle furnace at 350°C for 1 hour, then add it to 100mL of 10% sodium chloride solution and heat it in a water bath at 70°C for 2 hours; (b) Add 50mL of 20% to the sodium chloride solution Sodium hydroxide solution, heated to 80°C, sonicated, and stirred for 20 min; (c) Filter, put the activated kaolin in a beaker, rinse with deionized water until the solution is neutral, filter again, and place the kaolin at 80 After drying for 2 hours in a drying oven at ℃, grind and pass through a 50-mesh sieve;
[0037] Step S2: Mix nano-silica, albit...
Embodiment 2
[0049] A ceramic glaze made of the following raw materials by weight: 40 parts of nano silicon dioxide, 60 parts of kaolin, 20 parts of albite, 8 parts of magnesium oxide, 8 parts of sodium oxide, 30 parts of dolomite, 30 parts of limestone, 5 parts of pigments and fillers, 16 parts of modified additives, 60 parts of deionized water;
[0050] The ceramic glaze is made by the following method:
[0051] Step S1. Activation of kaolin: (a) Put the kaolin in a muffle furnace at 350°C for 1 hour, then add it to 100mL of 10% sodium chloride solution and heat it in a water bath at 70°C for 2 hours; (b) Add 50mL of 20% to the sodium chloride solution Sodium hydroxide solution, heated to 80°C, sonicated, and stirred for 20 min; (c) Filter, put the activated kaolin in a beaker, rinse with deionized water until the solution is neutral, filter again, and place the kaolin at 80 After drying for 2 hours in a drying oven at ℃, grind and pass through a 50-mesh sieve;
[0052] Step S2: Mix nano-sili...
Embodiment 3
[0057] A ceramic glaze made of the following raw materials by weight: 45 parts of nano-silica, 70 parts of kaolin, 25 parts of albite, 13 parts of magnesium oxide, 13 parts of sodium oxide, 45 parts of dolomite, 35 parts of limestone, 6 parts of pigments and fillers, 18 parts of modified additives, 65 parts of deionized water;
[0058] The ceramic glaze is made by the following method:
[0059] Step S1. Activation of kaolin: (a) Put the kaolin in a muffle furnace at 350°C for 1 hour, then add it to 100mL of 10% sodium chloride solution and heat it in a water bath at 70°C for 2 hours; (b) Add 50mL of 20% to the sodium chloride solution Sodium hydroxide solution, heated to 80°C, sonicated, and stirred for 20 min; (c) Filter, put the activated kaolin in a beaker, rinse with deionized water until the solution is neutral, filter again, and place the kaolin at 80 After drying for 2 hours in a drying oven at ℃, grind and pass through a 50-mesh sieve;
[0060] Step S2: Mix nano-silica, alb...
PUM
Property | Measurement | Unit |
---|---|---|
particle diameter | aaaaa | aaaaa |
Abstract
Description
Claims
Application Information
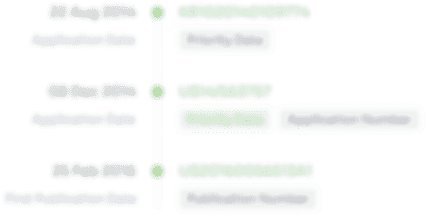
- R&D Engineer
- R&D Manager
- IP Professional
- Industry Leading Data Capabilities
- Powerful AI technology
- Patent DNA Extraction
Browse by: Latest US Patents, China's latest patents, Technical Efficacy Thesaurus, Application Domain, Technology Topic.
© 2024 PatSnap. All rights reserved.Legal|Privacy policy|Modern Slavery Act Transparency Statement|Sitemap