Welding wire for surfacing of composite carbide reinforced scraper and preparation method of welding wire
A composite carbide and scraper technology, applied in welding equipment, manufacturing tools, welding media, etc., can solve the problems of unusable, affecting the use effect, and harsh use environment, so as to improve the distribution of primary carbides, increase the hardness and Bending strength and effect of improving wear resistance
- Summary
- Abstract
- Description
- Claims
- Application Information
AI Technical Summary
Benefits of technology
Problems solved by technology
Method used
Image
Examples
preparation example Construction
[0042] The invention also provides a preparation method of a composite carbide reinforced scraper surfacing welding wire, and the specific steps are as follows:
[0043] Step 1: Weigh the following powders by mass percentage: 1~2% of graphene, 0.5~0.7% of Si powder, 1~3% of Mn powder, 60~65% of Cr powder, 2~3% of V powder, 2% of B powder ~3%, Ti powder 2~3%, CeO 2 The powder is 1-2%, the rest is Fe powder, and the sum of the mass percentages of the above components is 100%.
[0044] Step 2: The medicinal powder weighed in step 1 is placed in a vacuum heating furnace for heating, the heating temperature is 180-200 ° C, the holding time is 1-3 h, and the crystal water in the medicinal powder is removed; the dried medicinal powder is placed in the mixed powder. Fully mixed in the machine, the mixing time is 1 ~ 3h;
[0045] Step 3: Use the low carbon steel strip as the welding skin, use alcohol to remove the grease on the surface of the low carbon steel strip, wrap the powder prep
Embodiment 1
[0056] Step 1: Weigh the powders by mass percentage: graphene 1%, Si powder 0.5%, Mn powder 1%, Cr powder 60%, V powder 2%, B powder 2%, Ti powder 2%, CeO 2 1% powder, and the rest are Fe powder, and the sum of the mass percentages of the above components is 100%.
[0057] Among them, the particle size of Si powder, Mn powder, Cr powder and B powder are all 200 mesh, the particle size of the graphene is 10 μm, the CeO 2 It is nano-sized, the particle size is 100nm, and the purity of the powder is ≥99.90%;
[0058] Step 2: Place the medicine powder weighed in step 1 and heat it in a vacuum heating furnace, the heating temperature is 180 ° C, the holding time is 1h, and the crystal water in the medicine powder is removed; the dried medicine powder is placed in a powder mixer Carry out sufficient mixing, and the mixing time is 1h;
[0059] Step 3: Use the low carbon steel strip as the welding skin, use alcohol to remove the grease on the surface of the low carbon steel strip, wrap
Embodiment 2
[0073] Step 1: Weigh the powders by mass percentage: graphene 2%, Si powder 0.7%, Mn powder 3%, Cr powder 65%, V powder 3%, B powder 3%, Ti powder 3%, CeO 2 2% powder, the rest are Fe powder, and the sum of the above component mass percentages is 100%.
[0074] Among them, the particle size of Si powder, Mn powder, Cr powder and B powder are all 200 mesh, the particle size of the graphene is 10 μm, the CeO 2 It is nano-sized, the particle size is 100nm, and the purity of the powder is ≥99.90%;
[0075] Step 2: Place the medicine powder weighed in step 1 and heat it in a vacuum heating furnace, the heating temperature is 200 ° C, the holding time is 3h, and the crystal water in the medicine powder is removed; the dried medicine powder is placed in a powder mixer Carry out sufficient mixing, and the mixing time is 3h;
[0076] Step 3: Use the low carbon steel strip as the welding skin, use alcohol to remove the grease on the surface of the low carbon steel strip, wrap the powder
PUM
Property | Measurement | Unit |
---|---|---|
Thickness | aaaaa | aaaaa |
Width | aaaaa | aaaaa |
Thickness | aaaaa | aaaaa |
Abstract
Description
Claims
Application Information
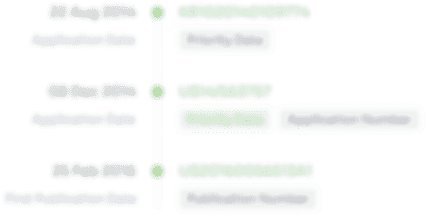
- R&D Engineer
- R&D Manager
- IP Professional
- Industry Leading Data Capabilities
- Powerful AI technology
- Patent DNA Extraction
Browse by: Latest US Patents, China's latest patents, Technical Efficacy Thesaurus, Application Domain, Technology Topic.
© 2024 PatSnap. All rights reserved.Legal|Privacy policy|Modern Slavery Act Transparency Statement|Sitemap