Gradient ceramic matrix composite material and preparation method thereof
A composite material and ceramic-based technology, which is applied in the field of gradient ceramic-based composite materials and its preparation, can solve the problems of high fiber volume fraction of prefabricated body, uneven distribution of ceramic components, high density of composite materials, etc. Excellent ablation performance and high activity
- Summary
- Abstract
- Description
- Claims
- Application Information
AI Technical Summary
Problems solved by technology
Method used
Examples
Example Embodiment
[0041] The embodiment of the present invention provides a preparation method of a gradient ceramic matrix composite material, and the preparation method includes:
[0042] (1) Combine ZrC ceramic powder and ZrB 2 The ceramic powder is mixed uniformly as a solid component, the phenolic resin and PVB resin are mixed uniformly as a liquid component, and the solid component and the liquid component are mixed uniformly to obtain a ceramic slurry;
[0043] (2) uniformly coating the ceramic slurry on at least N kinds of carbon cloths with different areal densities to obtain at least N kinds of prepregs;
[0044] (3) Lay up at least N kinds of prepregs, and then solidify to obtain carbon fiber preforms; wherein, the areal density of each layer of prepregs in the thickness direction of the carbon fiber preforms changes in a gradient, and in each prepreg include at least one layer of prepreg;
[0045] (4) cracking the carbon fiber preform to obtain a porous carbon / carbon intermediate;
Example Embodiment
[0086] Example 1
[0087] (1) Combine ZrC ceramic powder and ZrB 2 Ceramic powder (both particle size is 200~300nm) is mixed as solid component, phenolic resin and PVB resin (molecular weight 2000~3000g / mol) are mixed as liquid component, solid component and liquid component are mixed according to mass Mixing at a ratio of 20:80 to obtain ceramic slurry;
[0088] Among them, ZrC ceramic powder and ZrB in the solid component 2 The molar ratio of ceramic powder is 1:1; the mass fraction of PVB resin in the liquid component is 30%;
[0089] (2) Choose four areal densities of 240g / cm 2 , 250g / cm 2 , 260g / cm 2 and 270g / cm 2 4 kinds of prepregs (the corresponding mass fractions of ceramic slurry in the prepregs are 61% and 58% respectively) , 55%, 52%);
[0090] (3) The 4 kinds of prepregs are set to 240g / cm according to the carbon cloth surface density 2 , 250g / cm 2 , 260g / cm 2 , 270g / cm 2 , 260g / cm 2 , 250g / cm 2 , 240g / cm 2 Lay-up, then press, u
Example Embodiment
[0093] Example 2
[0094] Example 2 is basically the same as Example 1, except that:
[0095] In step (1), the mass ratio of solid component and liquid component is 30:70.
PUM
Property | Measurement | Unit |
---|---|---|
Particle size | aaaaa | aaaaa |
Particle size | aaaaa | aaaaa |
Areal density | aaaaa | aaaaa |
Abstract
Description
Claims
Application Information
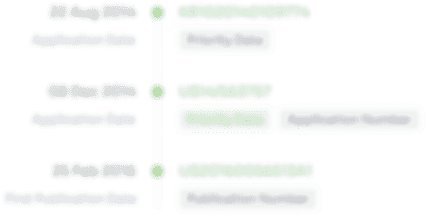
- R&D Engineer
- R&D Manager
- IP Professional
- Industry Leading Data Capabilities
- Powerful AI technology
- Patent DNA Extraction
Browse by: Latest US Patents, China's latest patents, Technical Efficacy Thesaurus, Application Domain, Technology Topic.
© 2024 PatSnap. All rights reserved.Legal|Privacy policy|Modern Slavery Act Transparency Statement|Sitemap