Preparation method of methyl vinyl ketone
A technology of methyl vinyl ketone and copper-based catalyst, which is applied in the field of preparation of methyl vinyl ketone, can solve problems such as complicated preparation steps, and achieve the effect of easy industrial implementation and large-scale production
- Summary
- Abstract
- Description
- Claims
- Application Information
AI Technical Summary
Problems solved by technology
Method used
Examples
Embodiment 1
[0027] The preparation process of dehydrogenation catalyst DH1 is as follows:
[0028] (1) Weigh 152g of copper nitrate, 80g of ytterbium nitrate and 109g of aluminum nitrate, dissolve them in 1 L of deionized water, and prepare solution A1. Weigh 30 g of potassium hydroxide and 12 g of potassium bicarbonate respectively, dissolve them in 1L of deionized water, and configure solution B1. Add 1L of deionized water into a 5L beaker, raise the temperature and maintain it at 95°C, add solutions A1 and B1 dropwise at the same time under the condition of continuous stirring, control the pH value to maintain around 9.0, and continue stirring for 2 h after the dropwise addition is completed , followed by static aging for 2 h, and filtered to obtain precipitate C1.
[0029] (2) Dry the precipitate C1 at 110°C for 24 h, then bake it at 400°C for 5 h, then add graphite powder with 3% of the weight of the precipitate as a lubricant, press it into a tablet, and then bake it at 400°C for 5...
Embodiment 2
[0033] The preparation process of dehydrogenation catalyst DH2 is as follows:
[0034] (1) Weigh 130g of copper nitrate, 175g of nickel nitrate and 86g of aluminum nitrate respectively, dissolve them in 1 L of deionized water, and prepare solution A2. Weigh 30 g of potassium hydroxide and 12 g of potassium bicarbonate respectively, dissolve them in 1L of deionized water, and configure solution B2. Add 1L of deionized water into a 5L beaker, raise the temperature and maintain it at 95°C, and add solution A2 and B2 dropwise at the same time under the condition of continuous stirring, keep the pH value at about 9.0, and continue stirring for 2 h after the dropwise addition is completed , followed by static aging for 2 h, and the precipitate C2 was obtained by filtration.
[0035] (2) Dry the precipitate C2 at 110°C for 24 h, then bake it at 400°C for 5 h, then add graphite powder with 3% of the weight of the precipitate as a lubricant, press it into a tablet, and then bake it at...
Embodiment 3
[0039] The preparation process of dehydrogenation catalyst DH3 is as follows:
[0040](1) Weigh 121g of copper nitrate, 147g of zinc nitrate and 140g of aluminum nitrate, dissolve them in 1 L of deionized water, and prepare solution A3. Weigh 30 g of potassium hydroxide and 12 g of potassium bicarbonate respectively, dissolve them in 1L of deionized water, and configure solution B3. Add 1L of deionized water into a 5L beaker, raise the temperature and maintain it at 95°C, add solutions A3 and B3 dropwise at the same time under the condition of continuous stirring, control the pH value to maintain around 9.0, and continue stirring for 2 h after the dropwise addition is completed , followed by static aging for 2 h, and the precipitate C3 was obtained by filtration.
[0041] (2) Dry the precipitate C3 at 110°C for 24 h, then roast at 400°C for 5 h, then add graphite powder with 3% of the weight of the precipitate as a lubricant, press into tablets, and then roast at 400°C for 5 ...
PUM
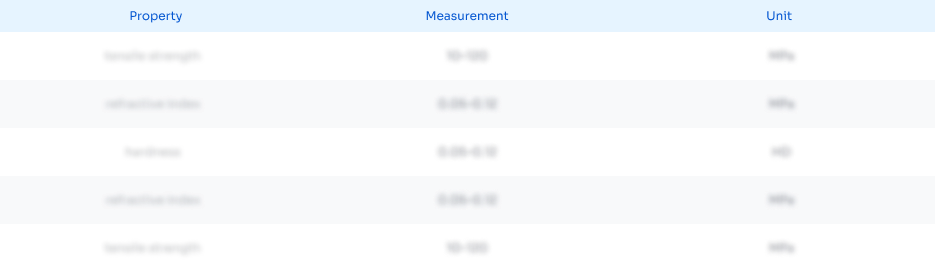
Abstract
Description
Claims
Application Information
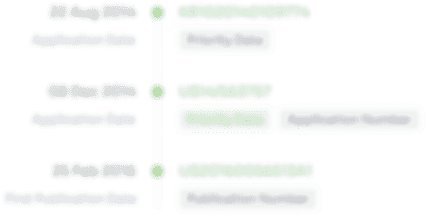
- R&D Engineer
- R&D Manager
- IP Professional
- Industry Leading Data Capabilities
- Powerful AI technology
- Patent DNA Extraction
Browse by: Latest US Patents, China's latest patents, Technical Efficacy Thesaurus, Application Domain, Technology Topic.
© 2024 PatSnap. All rights reserved.Legal|Privacy policy|Modern Slavery Act Transparency Statement|Sitemap