Grain-oriented electrical steel plate and preparation method thereof
A technology for oriented electrical steel sheets and steel sheets, which is applied in the improvement of process efficiency, metal material coating process, coating, etc., can solve the problems of noise improvement, transformer space factor and efficiency deterioration, etc., and achieves excellent insulation properties and iron loss. low effect
- Summary
- Abstract
- Description
- Claims
- Application Information
AI Technical Summary
Benefits of technology
Problems solved by technology
Method used
Image
Examples
preparation example Construction
[0041] figure 1 The flow chart of the preparation process of common grain-oriented electrical steel sheets is shown.
[0042] like figure 1 As shown, the annealing and pickling process (APL: Annealing & Pickling Line) is a step of removing the scale of the hot-rolled sheet, securing the cold-rollability, and precipitating and dispersing the inhibitor (AlN) of the hot-rolled sheet so as to contribute to the magnetism. Next, the cold rolling process is a step of rolling the hot-rolled sheet to the thickness of the final product and securing the crystal orientation favorable for the magnetic properties. In addition, the primary recrystallization annealing process is a step of forming primary recrystallization by removing carbon in the cold-rolled sheet through a decarburizing and nitriding annealing process (DNL: Decarburizing & Nitriding Line) and performing a nitridation reaction at an appropriate temperature. Next, a metal oxide layer (MgO) is formed in a high temperature annea
experiment example 1
[0107] Experimental Example 1: Properties by Type of Ceramic Precursor
Embodiment 1 to Embodiment 9
[0109] A slab was prepared, which included silicon (Si): 3.4 wt %, aluminum (Al): 0.03 wt %, manganese (Mn): 0.10 wt %, antimony (Sb): 0.05 wt %, and tin (Sn): 0.05 wt%, and the balance consists of Fe and other unavoidable impurities.
[0110] After heating the slab at 1150° C. for 220 minutes, it was hot-rolled with a thickness of 2.3 mm to prepare a hot-rolled sheet.
[0111] The hot-rolled sheet was heated to 1120° C., held at 920° C. for 95 seconds, then quenched in water and pickled, and then cold-rolled with a thickness of 0.23 mm to prepare a cold-rolled sheet.
[0112] The cold-rolled sheet is put into a furnace (furnace) maintained at 850 ° C, and the dew point temperature and oxidation energy are adjusted. In a mixed gas atmosphere of hydrogen, nitrogen and ammonia, decarburization nitriding and a recrystallization annealing are simultaneously performed to prepare decarburization annealing. rear steel plate.
[0113] After that, the annealing separator was not coated
PUM
Property | Measurement | Unit |
---|---|---|
Thickness | aaaaa | aaaaa |
Surface roughness | aaaaa | aaaaa |
Surface roughness | aaaaa | aaaaa |
Abstract
Description
Claims
Application Information
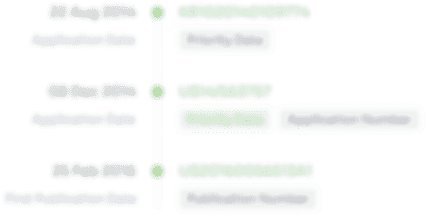
- R&D Engineer
- R&D Manager
- IP Professional
- Industry Leading Data Capabilities
- Powerful AI technology
- Patent DNA Extraction
Browse by: Latest US Patents, China's latest patents, Technical Efficacy Thesaurus, Application Domain, Technology Topic.
© 2024 PatSnap. All rights reserved.Legal|Privacy policy|Modern Slavery Act Transparency Statement|Sitemap