Polyimide composite diaphragm, preparation method thereof and lithium ion battery
A technology of polyimide-based film and composite diaphragm, which is applied in the direction of secondary batteries, battery pack components, circuits, etc., can solve the problems of poor electrolyte wettability and poor heat resistance in liquid retention rate, and improve cycle stability And the effects of service life, improved safety, and simple preparation method
- Summary
- Abstract
- Description
- Claims
- Application Information
AI Technical Summary
Problems solved by technology
Method used
Image
Examples
Embodiment 1
[0089] This embodiment provides a polyimide composite diaphragm, which includes a polyimide base film, a ceramic coating coated on one side of the polyimide base film, and a coating a meta-aramid polymer coating on the other side of the polyimide base film. The thickness of the polyimide composite diaphragm is 6 μm, the thickness of the ceramic coating is 2 μm, the thickness of the polymer coating is 2 μm, and the meta-aramid fiber glass in the meta-aramid coating The transition temperature is 400°C.
[0090] The preparation method comprises the following steps:
[0091] (1) will D 10 Particle size is 0.3μm, D 50 Particle size is 0.6μm, D 90 The particle size is 1.3μm and the specific surface area is 7m 230g boehmite (purity is 99.95%) and 45g deionized water per gram are stirred at high speed, the speed of stirring is 1000rpm, the time of stirring is 4h, and after stirring for 6h in the mode of magnetic stirring, ultrasonic dispersion 1h, at 30 After heating at ℃ for 0.5h,
Embodiment 2
[0095] This embodiment provides a polyimide composite diaphragm, which includes a polyimide base film, a ceramic coating coated on one side of the polyimide base film, and a coating a meta-aramid polymer coating on the other side of the polyimide base film. The thickness of the polyimide composite diaphragm is 8 μm, the thickness of the ceramic coating is 2.5 μm, the thickness of the polymer coating is 2.5 μm, and the meta-aramid in the meta-aramid coating The glass transition temperature is 320°C.
[0096] The preparation method comprises the following steps:
[0097] (1) will D 10 Particle size is 0.35μm, D 50 Particle size is 0.65μm, D 90 The particle size is 1.35μm and the specific surface area is 7.5m 2 35g boehmite / g and 70g deionized water were stirred at a high speed, the stirring rate was 1000rpm, the stirring time was 6h, and then stirred by magnetic stirring for 6h, ultrasonically dispersed for 1h, and heated at 35°C for 1.5h to After dissolving, add 2.5g propy
Embodiment 3
[0101] This embodiment provides a polyimide composite diaphragm, which includes a polyimide base film, a ceramic coating coated on one side of the polyimide base film, and a coating a meta-aramid polymer coating on the other side of the polyimide base film. The thickness of the polyimide composite diaphragm is 10 μm, the thickness of the ceramic coating is 2.2 μm, the thickness of the polymer coating is 2.2 μm, and the meta-aramid fiber in the meta-aramid coating The glass transition temperature is 260°C.
[0102] The preparation method comprises the following steps:
[0103] (1) will D 10 Particle size is 0.32μm, D 50 Particle size is 0.62μm, D 90 The particle size is 1.32μm and the specific surface area is 7.2m 2 20g alumina per gram and 60g deionized water were stirred at a high speed, the stirring rate was 800rpm, the stirring time was 9h, and then stirred by magnetic stirring for 6h, ultrasonically dispersed for 1h, heated at 20°C for 3h until dissolved Then add 1g of
PUM
Property | Measurement | Unit |
---|---|---|
Thickness | aaaaa | aaaaa |
Thickness | aaaaa | aaaaa |
Glass transition temperature | aaaaa | aaaaa |
Abstract
Description
Claims
Application Information
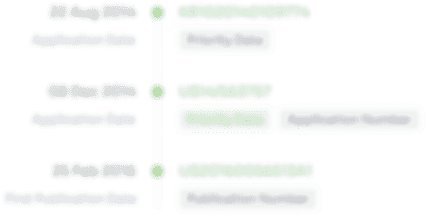
- R&D Engineer
- R&D Manager
- IP Professional
- Industry Leading Data Capabilities
- Powerful AI technology
- Patent DNA Extraction
Browse by: Latest US Patents, China's latest patents, Technical Efficacy Thesaurus, Application Domain, Technology Topic.
© 2024 PatSnap. All rights reserved.Legal|Privacy policy|Modern Slavery Act Transparency Statement|Sitemap