High-thixotropic poly(vinyl chloride) plastic sol
A polyvinyl chloride and plastisol technology, applied in the field of highly thixotropic polyvinyl chloride plastisol compositions, can solve problems such as high curing temperature and short storage period
- Summary
- Abstract
- Description
- Claims
- Application Information
AI Technical Summary
Benefits of technology
Problems solved by technology
Method used
Examples
Embodiment 1
[0033]First, 128 kg of dioctyl phthalate (purchased from Shanghai Solvent Factory) was mixed with 8.7 kg of dimer acid polyamide (trade name 305, purchased from Japan Sanwa Co.) and 8.7 kg of phenol-blocked hexylene diisocyanate. Then mix in 12 kg of dry bentonite. Then add 127 kilograms of polyvinyl chloride paste resin (trade name WP-62GP, purchased from Shanghai Tianyuan Chemical Factory) and 220 kilograms of calcium carbonate and disperse in a high-speed disperser for half an hour, and vacuum degassing after mixing for 3 hours is completed.
[0034] After storage for half a year, the polyvinyl chloride plastisol prepared above has little increase in viscosity (initial viscosity is 25000mPa.s / 25°C, viscosity is 50000mPa.s / 25°C after half a year), and the continued use performance remains unchanged. Apply the plastisol roller on the galvanized iron plate, the adhesive layer is 2mm thick, and invert for 3 minutes, the adhesive will not sag or flow. After curing at 160°C for
Embodiment 2
[0036] First mix 135 kg of dioctyl phthalate with 9 kg of dimer acid type polyamide (trade name 305) and 9 kg of phenol-blocked polymethylene polyphenylene isocyanate (PAPI), and then mix it into the dry gas phase two Silicon oxide 4 kg. Then add 140 kilograms of polyvinyl chloride paste resin (WP-62GP) and 216 kilograms of dry calcium carbonate and disperse in a high-speed disperser for half an hour. After mixing, vacuum defoaming is completed after 3 hours.
[0037] The polyvinyl chloride plastisol prepared above has little increase in viscosity after being stored for half a year (the initial viscosity is 35000mPa.s / 25°C, and the viscosity after half a year is 70000mPa.s / 25°C), and the continued use performance remains unchanged. The plastisol roll is coated on the galvanized iron plate with a thickness of 2 mm, and it is inverted for 3 minutes, and the rubber material does not sag or flow. After curing at 160°C for 10 minutes, the adhesive strength of the coating is 1.10N
Embodiment 3
[0039] First 135 kg of dioctyl phthalate was mixed with 9 kg of dimer acid type polyamide (305) and 9.1 kg of phenol-blocked trimerized TDI isocyanate, and then 4 kg of dry fumed silica was mixed. Then add 145 kilograms of polyvinyl chloride paste resin (WP-62GP) and 216 kilograms of dry calcium carbonate to disperse in a high-speed disperser for half an hour, and vacuum defoaming for 3 hours after mixing is completed.
[0040] After storage for half a year, the polyvinyl chloride plastisol prepared above has little increase in viscosity (initial viscosity is 30000mPa.s / 25°C, viscosity is 60000mPa.s / 25°C after half a year), and the continued use performance remains unchanged. The plastisol roll is coated on the galvanized iron plate with a thickness of 2 mm, and it is inverted for 3 minutes, and the rubber material does not sag or flow. After curing at 160°C for 10 minutes, the adhesive strength of the coating is 1.23N / mm 2 (steel-steel shear).
PUM
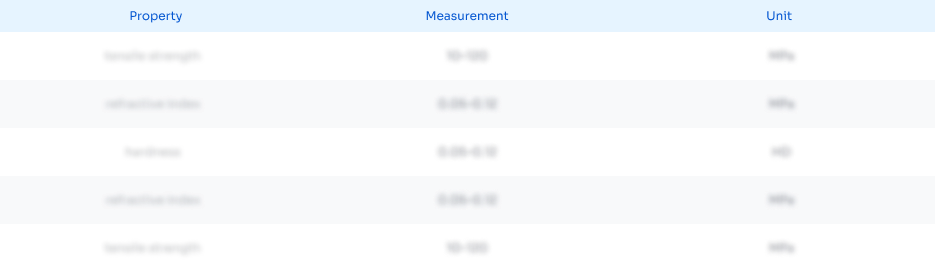
Abstract
Description
Claims
Application Information
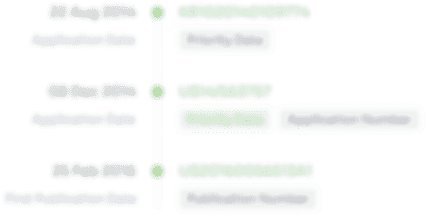
- R&D Engineer
- R&D Manager
- IP Professional
- Industry Leading Data Capabilities
- Powerful AI technology
- Patent DNA Extraction
Browse by: Latest US Patents, China's latest patents, Technical Efficacy Thesaurus, Application Domain, Technology Topic.
© 2024 PatSnap. All rights reserved.Legal|Privacy policy|Modern Slavery Act Transparency Statement|Sitemap