Hydrodynamic bearing device
- Summary
- Abstract
- Description
- Claims
- Application Information
AI Technical Summary
Benefits of technology
Problems solved by technology
Method used
Image
Examples
first embodiment
[0036]FIG. 1 is a sectional view of a hydrodynamic bearing device according to a first embodiment of the present invention. A shaft 2 is rotatably inserted into a bearing hole 1a of a sleeve 1, and a radial bearing surface having dynamic pressure generating grooves 3A and 3B constituted of pattern-shaped shallow grooves is provided at least one of an outer peripheral surface of the shaft 2 and an inner peripheral surface of the sleeve 1. A rotor hub 5 having a rotor magnet 4 in an inner periphery of its large diameter portion is mounted at one end (upper part in FIG. 1) side of the shaft 2, and a thrust flange 6 is integrally mounted at the other end (lower part in FIG. 1) side of the shaft 2 to be perpendicular to the shaft 2. A bearing surface at the lower end side of the thrust flange 6 opposes to a thrust plate 7, and the thrust plate 7 is fixed to the sleeve 1. A dynamic pressure generating groove 8A in a spiral or a herringbone pattern is formed on at least one of the surfaces of
second embodiment
[0052]FIG. 8 is a sectional view of a hydrodynamic bearing device according to a second embodiment of the present invention. A shaft 22 is rotatably inserted into a bearing hole 21a of a sleeve 21, and a radial bearing surface having dynamic pressure generating grooves 23A and 23B constructed by pattern-shaped shallow grooves is provided on at least one of an outer peripheral surface of the shaft 22 and an inner peripheral surface of the sleeve 21. A thrust bearing surface is formed at a lower end surface of the shaft 22 to be perpendicularly to the shaft 22, the thrust bearing surface is opposed to a thrust plate 24, the thrust plate 24 is fixed to the sleeve 21, a dynamic pressure generating groove 25 in a spiral or a herringbone pattern is formed on any one of the thrust bearing surface and the surface of the thrust plate 24, and a gap between the shaft 22 and the sleeve 21 and a gap between the shaft 22 and the thrust plate 24 are filled with oil 26 as the lubricant. The sleeve 21
PUM
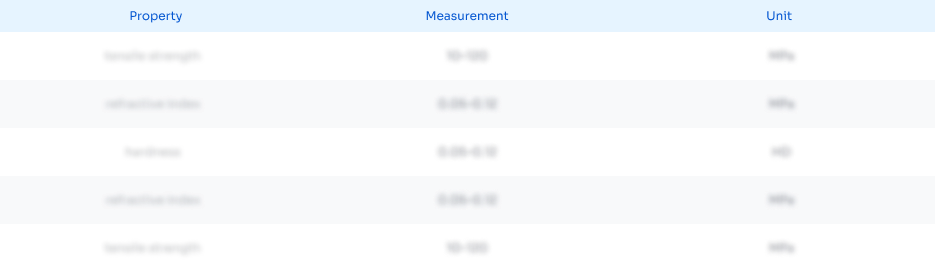
Abstract
Description
Claims
Application Information
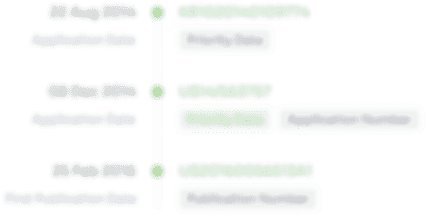
- R&D Engineer
- R&D Manager
- IP Professional
- Industry Leading Data Capabilities
- Powerful AI technology
- Patent DNA Extraction
Browse by: Latest US Patents, China's latest patents, Technical Efficacy Thesaurus, Application Domain, Technology Topic.
© 2024 PatSnap. All rights reserved.Legal|Privacy policy|Modern Slavery Act Transparency Statement|Sitemap