Organometallic compositions and coating compositions
a technology of organic compositions and compositions, applied in the direction of organic compounds/hydrides/coordination complexes, catalysts, physical/chemical process catalysts, etc., can solve the problems of low gloss coatings, low cure rate at low temperatures, and insufficient cure rate of coatings under high humidity or low temperature conditions, etc., to achieve excellent room temperature stability, excellent humidity resistance, and reduce yellowing
- Summary
- Abstract
- Description
- Claims
- Application Information
AI Technical Summary
Benefits of technology
Problems solved by technology
Method used
Image
Examples
examples
[0121]
TABLE 1Materials UsedProduct Description, ManufacturerALBESTER 3870OH Polyester, OH Number: 40,(Component A)Resolution, Specialty MaterialsVESTAGON BF 1540Polyisocyanate Uretdione Coating,(Component B)Hardener, % NCO: 15.2%, DegussaCorporationSipernat 50sFumed Silica, Degussa CorporationDisparlon PL-540Leveling Agent, King Industries, Inc.Ti-Pure-TiO2 R-900Titanium Dioxide, E.I. DuPontVESTAGON B 1400Caprolactam Blocked PolyisocyanateHardener, Degussa Corporation, %NCO: 12.5%BUTAFLOW BT-7170% DBTDL on Powder Carrier, EstronChemical Inc.Alcure 4470Triazole Blocked Polyisocyanate, NCOE.W.: 212, Resolution SpecialtyMaterialsAcrylamac HS 232-2980Acrylic Polyol, 80% N.V., OH E.W.: 793.8based on solution, Eastman ChemicalCompanyTrixene BI 7984HDI Trimer Blocked with MEKO, 75%N.V., NCO E.W.: 497.3 based onsolution, Baxenden, UKK-KAT XC-B221Bismuth Carboxylate, 20% Bi, KingIndustries, Inc.Trixene BI 7982HDI Trimer Blocked with 3,5-Dimethylpyrazole, 70% N.V., NCO E.W.:585.7 based on soluti
examples 1-4
[0124] Clear Non-Pigmented Powder Coatings Preparation.
[0125] Clear Non-Pigmented Powder Coatings: ALBESTER 3870 (component A), VESTAGON BF 1540 (component B), [Zn(1-Methylimidazole)2(Acetate)2] / Sipernat 50S (component C), and Disparlon PL-540 leveling agent were intimately mixed in an edge runner mill and the mixture was then homogenized in an extruder at temperatures up to a maximum of 130° C. After cooling, the extrudate was fractionated and ground with a pin mill to a particle size of <100 μm. The powder prepared in this way was applied with an electrostatic powder spraying unit at 60 kV to degreased iron panels to establish film thicknesses of approximately 60 μm, which were then baked in a circulating air drying cabinet at temperatures between 150° and 200° C.
[0126] Powder coating compositions for Examples 1-4 (amounts in % by weight):
TABLE 3Examples1234ALBESTER 387080.7280.7280.7280.72VESTAGON BF 154017.2817.2817.2817.28Disparlon PL-5402.002.002.002.00Zn(1-methylimidazole
examples 5-8
[0132] White Pigmented Powder Coatings Preparation.
[0133] White Pigmented Powder Coatings: ALBESTER 3870 (component A), VESTAGON BF 1540 (component B), [Zn(1-Methylimidazole)2(Acetate)2] / Sipernat 50S (component C), Ti-Pure-TiO2 R-900, and Disparlon PL-540 leveling agent were intimately mixed in an edge runner mill and the mixture was then homogenized in an extruder at temperatures up to a maximum of 130° C. After cooling, the extrudate was fractionated and ground with a pin mill to a particle size of <100 μm. The powder prepared in this way was applied with an electrostatic powder spraying unit at 60 kV to degreased iron panels to establish film thicknesses of approximately 60 μm, which were then baked in a circulating air drying cabinet at temperatures between 150° and 200° C.
[0134] Powder coating compositions for Examples 5-8 (amounts in % by weight):
TABLE 8Examples5678ALBESTER 387054.1954.1954.1954.19VESTAGON BF 154011.6011.6011.6011.60Ti-Pure-TiO2 R-90032.8932.8932.8932.89Dis
PUM
Property | Measurement | Unit |
---|---|---|
Temperature | aaaaa | aaaaa |
Temperature | aaaaa | aaaaa |
Temperature | aaaaa | aaaaa |
Abstract
Description
Claims
Application Information
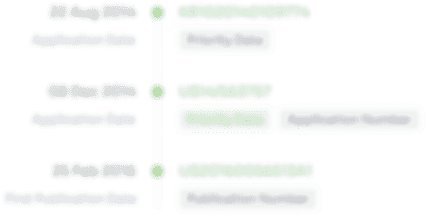
- R&D Engineer
- R&D Manager
- IP Professional
- Industry Leading Data Capabilities
- Powerful AI technology
- Patent DNA Extraction
Browse by: Latest US Patents, China's latest patents, Technical Efficacy Thesaurus, Application Domain, Technology Topic.
© 2024 PatSnap. All rights reserved.Legal|Privacy policy|Modern Slavery Act Transparency Statement|Sitemap