Aqueous reinforced rubber dispersions and their use for making latex foams
a technology of reinforced rubber and aqueous styrene, which is applied in the field of new aqueous styrene reinforced rubber dispersions, can solve the problems of high resilience of latex foam, unsuitable for all applications of latex foam, and inability to achieve multiphase graft copolymer dispersions, etc., and achieve the effect of stabilizing the foam structur
- Summary
- Abstract
- Description
- Claims
- Application Information
AI Technical Summary
Benefits of technology
Problems solved by technology
Method used
Image
Examples
reference example 1
Reinforcing Latex having a Ratio of Structural Units of Styrene to 1,3-butadien of 80 / 20
[0083] The reactor is charged with a solution of 1.75 g potassium oleate, 2.8 g sodium hydroxide and 0.350 g ammonium persulfate in 1225.0 g deionized water. The reactor is purged with nitrogen three times. The mixture is heated to 75 C and the temperature is kept constant. Then a feeding of 0.42 g ammonium persulfate dissolved in 7.98 g deionized water is started. The amount of the solution added per unit time is 0.420 g / min. The starting point of this feed is the time 0 minutes. At time 5 minutes the feed of 2 further components is started simultaneously. The first component consists of 26.950 g butadiene. The feeding rate is 1.797 g / min. The second component consists of 0.385 g tertiary-dodecyl mercaptan in 107.8 g styrene. The feeding rate is 7.212 g / min. At time 20 minutes the feeding of ammonium persulfate, butadiene and styrene is stopped. The inner reactor temperature is heated to 8
reference example 2
Reinforcing Latex having a Ratio of Structural Units of Styrene to 1,3-butadien of 70 / 30
[0087] The reactor is charged with a solution of 4.2 g potassium oleate, 10.5 g sodium hydroxide and 0.735 g ammonium persulfate in. 1925.0 g deionized water. The reactor is purged with nitrogen three times. The mixture is heated to 75° C. and the temperature is kept constant. Then a feeding of 0.875 g ammonium persulfate dissolved in 16.625 g deionized water is started. The amount of the solution added per unit time is 0.875 g / min. The starting point of this feed is the time 0 minutes. At time 5 minutes the feed of 2 further components is started simultaneously. The first component consists of 40.390 g butadiene. The feeding rate is 2.693 g / min. The second component consists of 94.220 g styrene. The feeding rate is 6.281 g / min. At time 20 minutes the feeding of ammonium persulfate, butadiene and styrene is stopped. The inner reactor temperature is heated to 81° C. within 15 minutes and the
reference example 3
Reinforcing Latex having a Ratio of Structural Units of Styrene to 1,3-butadien of 65 / 35
[0092] The reactor is charged with a solution of 4.2 g potassium oleate, 10.5 g sodium hydroxide and 0.735 g ammonium persulfate in 1925.0 g deionised water. The reactor is purged with nitrogen three times. The mixture is heated to 75° C. and the temperature is kept constant. Then a feeding of 0.875 g ammonium persulfate dissolved in 16.625 g deionised water is started. The amount of the solution added per unit time is 0.875 g / min. The starting point of this feed is the time 0 minutes. At time 5 minutes the feed of 2 further components is started simultaneously. The first component consists of 47.11 g butadiene. The feeding rate is 3.141 g / min. The second component consists of 87.5 g styrene. The feeding rate is 5.833 g / min. At time 20 minutes the feeding of ammonium persulfate, butadiene and styrene is stopped. The inner reactor temperature is heated to 81° C. within 15 minutes and then ke
PUM
Property | Measurement | Unit |
---|---|---|
Temperature | aaaaa | aaaaa |
Temperature | aaaaa | aaaaa |
Temperature | aaaaa | aaaaa |
Abstract
Description
Claims
Application Information
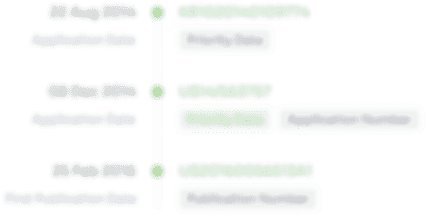
- R&D Engineer
- R&D Manager
- IP Professional
- Industry Leading Data Capabilities
- Powerful AI technology
- Patent DNA Extraction
Browse by: Latest US Patents, China's latest patents, Technical Efficacy Thesaurus, Application Domain, Technology Topic.
© 2024 PatSnap. All rights reserved.Legal|Privacy policy|Modern Slavery Act Transparency Statement|Sitemap