Polyimide tube, process for producing the same and fixing belt
- Summary
- Abstract
- Description
- Claims
- Application Information
AI Technical Summary
Benefits of technology
Problems solved by technology
Method used
Image
Examples
example 1
[0111]Carbon nanotubes and boron nitride (“MBN-010T” manufactured by Mitsui Chemicals, Inc.; graphite-structure BN; specific gravity: 2.27) were added to U varnish S (polyimide precursor varnish) respectively in 15 volume percent and 15 volume percent relative to the total volume of the solid content (the volume of the solid content in the varnish is defined as 100 volume percent). The resultant mixture was pre-stirred with a stirrer, mixed with a triple roll mill, and subsequently subjected to vacuum degassing. Thus, a polyimide varnish containing the above-described components was prepared.
[0112]A core member used was an aluminum cylinder having an outer diameter of 20 mm the outer surface of which was coated with ceramic. A nozzle (discharge opening) attached to the supply part of a dispenser was made in contact with the outer surface of the core member.
[0113]The polyimide varnish was coated over the core member by supplying the polyimide varnish at a constant rate to the outer surf
example 2
[0115]Carbon nanotubes were added to a polyimide precursor varnish that was a mixture of U varnish S and Pyre ML in 90:10 (proportion by weight), in 25 volume percent relative to the total volume of the solid content. The resultant mixture was pre-stirred with a stirrer, mixed with a triple roll mill, and subsequently subjected to vacuum degassing. Thus, a polyimide varnish containing the above-described components was prepared. A polyimide tube was prepared under the same conditions as in EXAMPLE 1 except that the thus-prepared polyimide varnish was used. This polyimide tube was subjected to the same measurements and tests as in EXAMPLE 1. The results are shown in Table I.
example 3
[0116]A polyimide tube was prepared under the same conditions as in EXAMPLE 2 except that the amount of the carbon nanotubes was made 30 volume percent relative to the total volume of the solid content. This polyimide tube was subjected to the same measurements and tests as in EXAMPLE 1. The results are shown in Table I.
PUM
Property | Measurement | Unit |
---|---|---|
Thickness | aaaaa | aaaaa |
Percent by volume | aaaaa | aaaaa |
Percent by volume | aaaaa | aaaaa |
Abstract
Description
Claims
Application Information
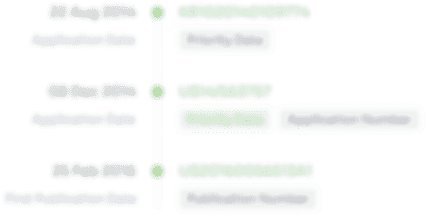
- R&D Engineer
- R&D Manager
- IP Professional
- Industry Leading Data Capabilities
- Powerful AI technology
- Patent DNA Extraction
Browse by: Latest US Patents, China's latest patents, Technical Efficacy Thesaurus, Application Domain, Technology Topic.
© 2024 PatSnap. All rights reserved.Legal|Privacy policy|Modern Slavery Act Transparency Statement|Sitemap