Electrically conductive composition and fabrication method thereof
a technology of electrical conductivity and composition, applied in the direction of oxide conductors, non-metal conductors, conductors, etc., can solve the problems of low conductivity of electrical components, inability to solder polymer-type flexible electronic materials,
- Summary
- Abstract
- Description
- Claims
- Application Information
AI Technical Summary
Benefits of technology
Problems solved by technology
Method used
Image
Examples
example 1
[0042]An organic acid silver (C7H15COOAg) compound of 39.8 wt % was dissolved in a solvent of xylene of 59.7 wt % and then uniformly mixed with multi-walled nanometer scale carbon tubes (MWCNT) of 0.5 wt % to form a mixture of the Example 1. Then, the mixture of the Example 1 was coated on a substrate made of polyethylene terephthalate (PET) by a spin coating process to fabricate an electrically conductive film of the Example 1. The fabrication condition of the electrically conductive film of the Example 1 was implemented by a heat process consisting of a background temperature of 120° C. and an auxiliary energy of far-infrared light to perform a sintering process.
examples 2-3
[0044]Organic acid silver (C7H15COOAg) compounds of 39.8 wt % and 38.1 wt % were dissolved in solvents of xylene of 59.7 wt % and 57.1 wt %, respectively, and then uniformly mixed with multi-walled nanometer scale carbon tubes of 0.5 wt % and 4.8 wt %, respectively, to form mixtures of the Examples 2-3. Then, the mixtures of the Examples 2-3 were coated on a substrate made of PET by a spin coating process to fabricate electrically conductive films of the Examples 2-3. The fabrication conditions of the electrically conductive films of the Examples 2-3 were implemented by a heat process of a background temperature of 130-150° C. to perform a sintering process. The compositions, the fabrication conditions and the sheet resistances of the electrically conductive films of the Examples 2-3 are shown in Table 1.
examples 4-7
[0051]Organic acid silver (C7H15COOAg) compounds of 39.7-49.8 wt % were dissolved in solvents of tolene respectively, and then uniformly mixed with multi-walled nanometer scale carbon tubes (MWCNT) of 0.5-0.8 wt %, respectively, to form mixtures of the Examples 4-7. Then, the mixtures of the Examples 4-7 were coated on a substrate made of PET by a spin coating process to fabricate electrically conductive films of the Examples 4-7. The fabrication conditions of the electrically conductive films of the Examples 4-7 were implemented by a heat process of a background temperature of 110-150° C. and an auxiliary energy of far-infrared light to perform a sintering process. The compositions, the fabrication conditions and the sheet resistances of the electrically conductive films of the Examples 4-7 are shown in Table 3.
[0052]Table 3 displays the compositions, the fabrication conditions and the sheet resistances of the electrically conductive films of Examples 4-7.
electricallysolution composit
PUM
Property | Measurement | Unit |
---|---|---|
Temperature | aaaaa | aaaaa |
Temperature | aaaaa | aaaaa |
Percent by mass | aaaaa | aaaaa |
Abstract
Description
Claims
Application Information
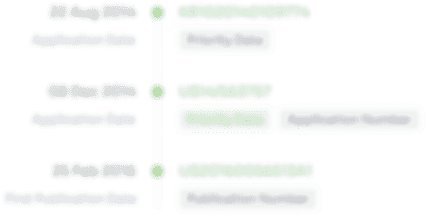
- R&D Engineer
- R&D Manager
- IP Professional
- Industry Leading Data Capabilities
- Powerful AI technology
- Patent DNA Extraction
Browse by: Latest US Patents, China's latest patents, Technical Efficacy Thesaurus, Application Domain, Technology Topic.
© 2024 PatSnap. All rights reserved.Legal|Privacy policy|Modern Slavery Act Transparency Statement|Sitemap