Hardenable synthetic resin comprising considerable proportions of cyclic carbonate groups, as well as/and cyclocarbonate-resin-based fixing systems, the production and use thereof
- Summary
- Abstract
- Description
- Claims
- Application Information
AI Technical Summary
Benefits of technology
Problems solved by technology
Method used
Image
Examples
example 1
General Working Procedure I: Synthesis of Cyclic Carbonate Resins Using the Example of the 4,4′-diphenylmethanediurethane Diglycerol Carbonate with Trimethylolpropane Triglycidyl Ether as Reactive Diluent
[0099]Trimethylolpropane triglycidyl ether and glycerol carbonate—in the amounts indicated in Table 1 (Example 3)—are introduced into a 250 ml glass flask having a reflux condenser with a drying tube, stirrer, dropping funnel and thermometer and heated in an oil bath at 60° C. The “PMDI” is slowly added dropwise to the reaction mixture so that the temperature does not rise above 80° C. Once the addition of the “PMDI” is complete, stirring is carried out at 80° C. to complete the reaction. Complete reaction (freedom from isocyanate groups detectable by IR spectroscopy) is checked by means of FT-IR.
example 2
General Working Procedure II: Alternative Method of Synthesising Cyclic Carbonate Resins Using the Example of the 4,4′-diphenylmethanediurethane Diglycerol Carbonate with Trimethylolpropane Triglycidyl Ether and Neopentyl Glycol Diglycidyl Ether as Reactive Diluent Mixture
[0100]Trimethylolpropane triglycidyl ether, neopentyl glycol diglycidyl ether and glycerol carbonate in the amounts indicated in Table 3 (Example 4) are introduced into a 120 ml plastics beaker having a screw closure. After thorough intermixing, the “PMDI” is added at room temperature and mixing is carried out again until a striation-free appearance is obtained. Then the plastics beaker containing the reaction mixture is stored at 40° C. in order to complete the reaction. Complete reaction (freedom from isocyanate groups detectable by IR spectroscopy) is checked by means of FT-IR.
example 3
Formulations for Carbonate Resins I
[0101]The formulation for the resins prepared according to Example 1 is as follows:
TABLE 1Formulation for carbonate resins with trimethylolpropane triglycidylether as reactive diluent (here: CVV-F-1 with isocyanate orcarbonate fct.: 2.2)ItemWeight introduced m [g]% by weightTrim57.8160.00Glycerol carbonate18.5419.24“PMDI”20.0020.76“PMDI” is a mixture of MDI (isocyanate functionality 2) and PMDI (isocyanate functionality 3.2) and / or monofunctional isocyanate (isocyanate functionality 1.0) according to Table 2.MDI: diphenylmethane diisocyanate isomeric mixture, molecular weight 250 g / mol, isocyanate functionality 2 (manufacturer's data)PMDI: diphenylmethane diisocyanate with isomers and higher-functional homologues, molecular weight 430 g / mol, isocyanate functionality 3.2 (manufacturer's data)p-TSI: p-toluenesulphonyl isocyanate, molecular weight 197.21 g / mol, isocyanate functionality 1Trim: trimethylolpropane triglycidyl ether (technical produc
PUM
Property | Measurement | Unit |
---|---|---|
Molar mass | aaaaa | aaaaa |
Molecular weight | aaaaa | aaaaa |
Content | aaaaa | aaaaa |
Abstract
Description
Claims
Application Information
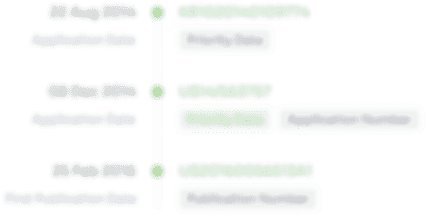
- R&D Engineer
- R&D Manager
- IP Professional
- Industry Leading Data Capabilities
- Powerful AI technology
- Patent DNA Extraction
Browse by: Latest US Patents, China's latest patents, Technical Efficacy Thesaurus, Application Domain, Technology Topic.
© 2024 PatSnap. All rights reserved.Legal|Privacy policy|Modern Slavery Act Transparency Statement|Sitemap