Oriented polypropylene films for adhesive tape
a polypropylene film and adhesive tape technology, applied in the direction of film/foil adhesives, other domestic articles, synthetic resin layered products, etc., can solve the problems of uncontrollable tearing or ripping, damage to the film, and less aesthetic appeal of the resultant severed edg
- Summary
- Abstract
- Description
- Claims
- Application Information
AI Technical Summary
Benefits of technology
Problems solved by technology
Method used
Image
Examples
examples 1 – 4
Examples 1–4
[0141]The appropriate resin mixture was fed into the feed hopper of a 4.45 cm single screw extruder manufactured from H.P.M (Mt. Gilead, Ohio) having an extruder barrel temperature adjusted to produce a stable homogeneous melt of about 250–260° C. The polypropylene melt was extruded through a 17.8 cm single manifold sheet die onto a rotating water cooled steel casting wheel which had about 50–60° C. water circulating through it. The cast sheet was next passed through a quenching water bath maintained at about 30° C. to produce a cast sheet having a thickness of about 0.16 cm.
[0142]Sequentially biaxially oriented polypropylene biaxially oriented substrates were prepared by a process known as the sequential tenter process. The cast sheet was passed over a first series of heating rolls maintained internally from about 127° C. to 136° C., and then stretched between two nipped drawing rolls rotating at different speeds to attain a first draw ratio of 5.0:1 in extrusion or castin
examples 5 – 7
Examples 5–7
[0143]Simultaneously biaxially oriented polypropylene Examples 5–7 were prepared by a process known as the simultaneous tenter process. First, the appropriate resin mixture was extruded to produce a stable homogeneous melt having a melt temperature of about 257° C. The polypropylene melt was cast onto a water cooled steel casting wheel rotating at about 10 meters per minute which had about 11° C. water circulating through it. The cast sheet was next passed through a quenching water bath maintained at about 20° C. to produce a cast sheet having a thickness of about 0.15–0.2 cm.
[0144]The cast film was simultaneous stretched in longitudinal and transverse directions using a diverging spindle simultaneous biaxial orienting tenter equipped with 7:1 stretching spindles, at a line speed of 80–85 meters per minute and a stretching temperature of about 175–180° C. to a final balanced area stretching ratio of about 50:1.
examples 8 – 16
Examples 8–16
[0145]Examples 8–16 were cast as described above in Examples 1–4.
[0146]Examples 8–9 were simultaneously stretched in two perpendicular directions using a laboratory two-way film stretching machine known as a frame or batch stretcher as follows. The cast film sheet of 0.16 cm thickness was cut into square tablets of 6.83 cm on a side and held in the stretching oven of the batch stretcher by edgewise gripping with a series of clips to leave a stretchable sample of 5.08 cm on a side. The tablet was pre-heated for 90 seconds at 155° C., and stretched at a rate of about 300% / second in the reference direction and about 250% / second in the direction perpendicular to the first direction to a final area stretch ratio of about 40:1. Samples were immediately removed from the stretching machine to cool. The film had a nominal thickness of about 0.030 cm. The film was slit into useful sample widths using a razor blade cutter equipped with fresh blades.
[0147]Examples 10–16 were prepa
PUM
Property | Measurement | Unit |
---|---|---|
Fraction | aaaaa | aaaaa |
Fraction | aaaaa | aaaaa |
Fraction | aaaaa | aaaaa |
Abstract
- A) at least one isotactic polypropylene homopolymer “A” having a weight average molecular weight of at least 350,000 grams/mole and melt a flow rate of about 0.5–8 grams/10 minutes, more preferably about 0.5–5 grams/10 minutes; with
- B) at least one isotactic polypropylene homopolymer “B” having a weight average molecular weight of at least 100,000 grams/mole and a melt flow rate greater than 8 grams/10 minutes, and preferably greater than about 20 grams/10 minutes, and more preferably greater than about 50 grams/10 minutes.
Description
Claims
Application Information
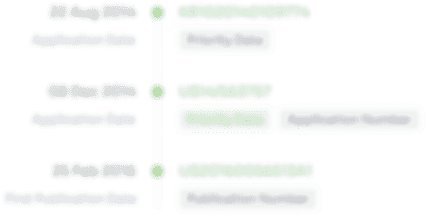
- R&D Engineer
- R&D Manager
- IP Professional
- Industry Leading Data Capabilities
- Powerful AI technology
- Patent DNA Extraction
Browse by: Latest US Patents, China's latest patents, Technical Efficacy Thesaurus, Application Domain, Technology Topic.
© 2024 PatSnap. All rights reserved.Legal|Privacy policy|Modern Slavery Act Transparency Statement|Sitemap