Electromagnetic foam absorption wedge material and its making technology
A technology of electromagnetic wave absorption and preparation process, which is applied in the direction of electrical components, magnetic/electric field shielding, shielding, etc., can solve problems such as difficult construction, bonding construction, and short service life, achieve uniform distribution of wave absorbing agents, and improve production efficiency , the effect of solving fire hazards
- Summary
- Abstract
- Description
- Claims
- Application Information
AI Technical Summary
Benefits of technology
Problems solved by technology
Method used
Image
Examples
preparation example Construction
[0029] A preparation process of electromagnetic wave-absorbing foam wedge material is as follows:
[0030] a. Preparation of resole phenolic resin as basic raw material.
[0031] b. The expandable phenolic resin made of resole phenolic resin, emulsifier, foaming agent and wave absorbing agent is A component, and the curing agent of inorganic acid and organic acid mixed to form the expandable phenolic resin is B group point.
[0032] c. A component and B component are mixed and poured into the wedge cavity.
[0033] d. The mold cavity temperature is controlled at 50-70°C for foam molding; the foam body is cured in the mold cavity for 60-90 minutes.
[0034] The formula of expandable phenolic resin is proportioned by weight as resole phenolic resin: emulsifier: foaming agent: wave absorbing agent=100: 2~5: 5~10: 3~10; The optimal proportioning of formula proportioning by weight is resole phenolic resin: emulsifier: whipping agent: wave absorbing agent=100: 3: 6: 8; The formula p
Embodiment 1
[0037] In the preparation process of the above-mentioned H500 type electromagnetic wave-absorbing foam wedge material:
[0038] (1) proportioning by weight
[0039] Preparation of component A: 100 parts of resole phenolic resin, 2 to 5 parts of emulsifier (hard foam silicone oil), 5 to 10 parts of foaming agent (pentane), 5 to 10 parts of wave absorbing agent and stir under a high-speed stirring device It is formulated into a foamable phenolic resin in half an hour.
[0040] Preparation of component B: water: p-toluenesulfonic acid: sulfuric acid = 1:1:1
[0041] (2) Put the H500 wedge mold in a drying room at 50-70°C, so that the temperature of the mold reaches 50-70°C.
[0042] (3) According to the ratio of expandable phenolic resin:curing agent=100:15, it is injected into the wedge cavity through a reaction injection molding machine.
[0043] (4) The foam body is matured in the mold cavity for 60-90 minutes to form.
[0044] (5) After the wedge is stripped from the mold, a
Embodiment 2
[0049] In the preparation process of the aforementioned H700 type electromagnetic wave-absorbing foam wedge material:
[0050] (1) Proportioning by weight parts:
[0051] Preparation of component A: 100 parts of resole phenolic resin, 2 to 5 parts of emulsifier, 5 to 10 parts of foaming agent, 5 to 10 parts of wave absorbing agent, and stir for half an hour under a high-speed stirring device to prepare a foamable phenolic resin .
[0052] In the present embodiment, the optimal proportioning in parts by weight:
[0053] Preparation of component A: 100 parts of resole phenolic resin, 3 parts of emulsifier, 8 parts of foaming agent, and 7 parts of wave absorbing agent were stirred under a high-speed stirring device for half an hour to prepare a foamable phenolic resin.
[0054] Preparation of component B: water: p-toluenesulfonic acid: sulfuric acid = 1:1:1.
[0055](2) Put the H700 wedge mold in a drying room at 50-70°C, so that the temperature of the mold reaches 50-70°C.
[0
PUM
Property | Measurement | Unit |
---|---|---|
Density | aaaaa | aaaaa |
Compressive strength | aaaaa | aaaaa |
Abstract
Description
Claims
Application Information
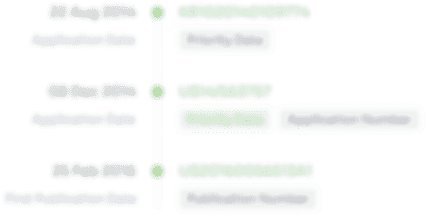
- R&D Engineer
- R&D Manager
- IP Professional
- Industry Leading Data Capabilities
- Powerful AI technology
- Patent DNA Extraction
Browse by: Latest US Patents, China's latest patents, Technical Efficacy Thesaurus, Application Domain, Technology Topic.
© 2024 PatSnap. All rights reserved.Legal|Privacy policy|Modern Slavery Act Transparency Statement|Sitemap