Method for preparing tin-nickel alloy of cathode materials of lithium ion battery by electrolyzing melted salt
A technology for lithium-ion batteries and negative electrode materials, applied in battery electrodes, electrode manufacturing, circuits, etc., can solve problems such as performance degradation, achieve the effects of reducing energy consumption, accelerating electrolytic reaction speed, and reducing production costs
- Summary
- Abstract
- Description
- Claims
- Application Information
AI Technical Summary
Problems solved by technology
Method used
Image
Examples
Example Embodiment
[0023] Example 1
[0024] Will analyze pure NiO and SnO 2 The powder is mixed with a molar ratio of 3:4, 3-10wt% of graphite powder is added, wet milled in a ball mill for 3 hours, taken out and dried, weighed 2.5g of the sample, and then pressed the powder to a diameter of 10mm under 30MPa. A cylinder with a height of 3.5mm and sintered at 850~1250℃ for 2~4 hours to obtain an oxide sintered sheet; the oxide sintered sheet is hung on the iron-chromium-aluminum wire, and the periphery is wrapped with iron-chromium-aluminum wire as Cathode: A high-purity graphite rod is used as the anode. Insert it into CaCl 2 In an alumina crucible mixed with NaCl molten salt, under the protection of Ar gas, control the voltage to 2.3~3.2V for electrolysis, the electrolysis temperature is 600~750℃, after 6~10 hours of electrolysis, stop the electrolysis; cool in an inert atmosphere Then rinse with distilled water and dry, the product is pure phase Ni 3 Sn 4 alloy.
[0025] Will be prepared Ni 3 Sn 4
Example Embodiment
[0026] Example 2
[0027] Will analyze pure NiO and SnO 2 The powder is mixed with a molar ratio of 1:1, and 5-15wt% CaCO is added 3 , Wet-grind in a ball mill for 3 hours, take out and dry, then weigh 2.5g of the sample, press the powder into a cylinder with a diameter of 10mm and a height of 3.5mm under 30MPa, and sinter it at 850~1250℃ for 3~8 After hours, the oxide sintered sheet is obtained; the oxide sintered sheet is suspended on the iron-chromium-aluminum wire, and the periphery is wrapped with the iron-chromium-aluminum wire as the cathode; and the high-purity graphite rod is used as the anode. Insert it with CaCl 2 In an alumina crucible mixed with NaCl molten salt, under the protection of Ar gas, control the voltage to 2.0~3.2V for electrolysis, the electrolysis temperature is 650~780℃, after 5~8 hours of electrolysis, stop the electrolysis; cool in an inert atmosphere Then rinse with distilled water and dry, the product is Ni 3 Sn 4 / Ni 3 Sn 2 Alloy composite.
[0028]
Example Embodiment
[0029] Example 3
[0030] Will analyze pure NiO and SnO 2 Mix the powder with a molar ratio of 2:1, add 3-15wt% starch, wet-grind in a ball mill for 3 hours, take out and dry, then weigh 2.5g of the sample, and press the powder into a diameter of 10mm under 30MPa. 3.5mm cylinder, and sinter it at 850~1250℃ for 2~4 hours to obtain oxide sintered sheet; hang the oxide sintered sheet on molybdenum wire and wrap the periphery with molybdenum wire as the cathode; adopt high purity Graphite rods are used as anodes. Insert it into CaCl 2 In an alumina crucible mixed with NaCl molten salt, under the protection of Ar gas, control the voltage to 2.0~3.2V for electrolysis, the electrolysis temperature is 600~780℃, after 8~16 hours of electrolysis, stop the electrolysis; cool in an inert atmosphere Then rinse with distilled water and dry, the product is Ni / Ni 3 Sn 4 / Ni 3 Sn 2 Alloy composite.
[0031] The prepared Ni / Ni 3 Sn 4 / Ni 3 Sn 2 The alloy compound adds 10wt% conductive agent a
PUM
Property | Measurement | Unit |
---|---|---|
Diameter | aaaaa | aaaaa |
Abstract
Description
Claims
Application Information
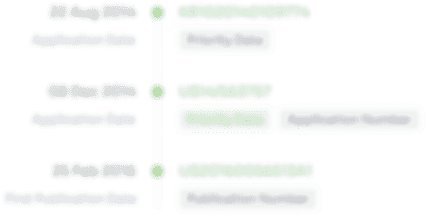
- R&D Engineer
- R&D Manager
- IP Professional
- Industry Leading Data Capabilities
- Powerful AI technology
- Patent DNA Extraction
Browse by: Latest US Patents, China's latest patents, Technical Efficacy Thesaurus, Application Domain, Technology Topic.
© 2024 PatSnap. All rights reserved.Legal|Privacy policy|Modern Slavery Act Transparency Statement|Sitemap