Preparation method of methyl phenyl chlorosilane
A technology of phenylmethyldichlorosilane and methyltrichlorosilane, which is applied in the field of organosilicon material synthesis, can solve the problems of limited industrial application, difficult product separation, difficult separation and purification, etc., and achieve good industrial application prospects and reaction conditions Controllable and solve the effect of many side effects
- Summary
- Abstract
- Description
- Claims
- Application Information
AI Technical Summary
Problems solved by technology
Method used
Examples
preparation example Construction
[0018] The preparation process of phenylmethyldichlorosilane: in N 2 Or under the protection of Ar, in a 500 mL reaction kettle, add Mg chips (0.28 mol) and solvent (can be taken from ethylene glycol dimethyl ether, 1,4-dioxane, diethyl ether, tetrahydrofuran, methyl tetrahydrofuran , n-butyl ether, methylal or toluene), raise the temperature to 50-100 °C in the kettle, add chlorobenzene (0.25mol) dropwise, after the dropwise addition, the micro-boiling reaction keeps reflux for 2-5 hours, and then stop the reaction , GC detection of by-products ≤ 0.01%. in N 2 Or under the protection of Ar, the MeSiCl 3 (0.25 mol), the solvent was added in a 500ml reaction kettle; after the Grignard reagent prepared above——phenylmagnesium chloride was lowered to normal temperature, it was transferred to the dropping funnel; 5h. The reaction liquid is filtered and washed, and then the solvent is distilled, and the 60-65°C / 300Pa fraction is collected by rectification under reduced pressure,
Embodiment 1
[0022] in N 2 Or under the protection of Ar, in a 500 mL reaction kettle, add Mg scraps (0.28 mol) and THF (100 mL) in sequence, raise the temperature to 50-66 ℃ in the kettle, add chlorobenzene (0.25 mol) dropwise, after the dropwise addition, micro The boiling reaction was kept under reflux for 2-5h, and the reaction was stopped. The by-product was detected by GC ≤0.01%, and a THF solution of phenylmagnesium chloride was obtained. N 2 Or under the protection of Ar, the MeSiCl 3 (0.25 mol), THF (100 ml) was added to a 500ml reactor. After the phenylmagnesium chloride prepared above is lowered to normal temperature, N 2 Or under the protection of Ar, transfer to the dropping funnel; add the Grignard reagent dropwise, and keep reflux for 2-5 hours after the dropwise addition. The reaction solution was filtered to obtain the magnesium salt (MgCl 2 (THF) 2 ), after washing with THF, directly distill THF, the recovery rate of THF is greater than 95%, rectification under reduced
Embodiment 2
[0024] in N 2 Or under the protection of Ar, in a 500 mL reaction kettle, add Mg chips (0.28 mol), THF (40 mL) and MePh (80 mL) in sequence, raise the temperature to 50-100 ℃ in the kettle, add PhCl (0.25 mol) dropwise , After the dropwise addition, the slightly boiling reaction was kept under reflux for 2-5 hours, the reaction was stopped, and the by-product was detected by GC ≤ 0.01%, and phenylmagnesium chloride was obtained. N 2 Or under the protection of Ar, the MeSiCl 3 (0.25 mol), THF (100 ml) was added to a 500ml reactor. After the Grignard reagent prepared above dropped to normal temperature, N 2 Or under the protection of Ar, transfer to the dropping funnel; add the Grignard reagent dropwise, and keep reflux for 2-5 hours after the dropwise addition. The reaction solution was filtered to obtain the magnesium salt (MgCl 2 (THF) 2 ), after washing, directly distill THF and MePh, the rate of recovery is greater than 97%, rectification under reduced pressure obtains p
PUM
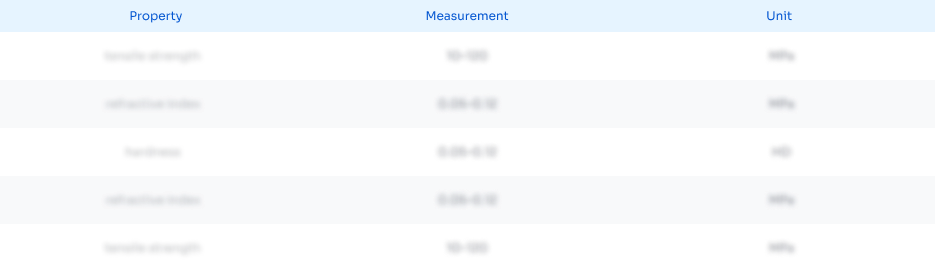
Abstract
Description
Claims
Application Information
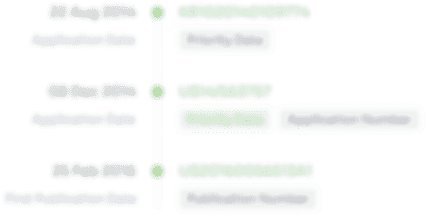
- R&D Engineer
- R&D Manager
- IP Professional
- Industry Leading Data Capabilities
- Powerful AI technology
- Patent DNA Extraction
Browse by: Latest US Patents, China's latest patents, Technical Efficacy Thesaurus, Application Domain, Technology Topic.
© 2024 PatSnap. All rights reserved.Legal|Privacy policy|Modern Slavery Act Transparency Statement|Sitemap