Connection method for carbon fiber yarns and metal sheet for heating
一种碳纤维丝、连接方法的技术,应用在加热元件、欧姆电阻加热零部件等方向,能够解决烧蚀、连接处温度高、易被氧化等问题,达到避免电阻过大、提高性能稳定、方法科学合理的效果
- Summary
- Abstract
- Description
- Claims
- Application Information
AI Technical Summary
Problems solved by technology
Method used
Examples
Embodiment 1
[0013] The present invention operates according to the following steps:
[0014] (1) Joint stock: 5 bundles of adjacent carbon fiber filaments at the end of the carbon fiber cloth are combined into one strand;
[0015] (2) Glue coating: evenly apply conductive glue mixed with curing agent at the contact between the ply carbon fiber filament and the metal sheet; the curing agent used is dimethylimidazole, and the conductive glue is bisphenol A epoxy resin mixed with silver powder;
[0016] (3) Felt wrapping: Wrap a layer of thin carbon fiber felt on the surface of the carbon fiber filament coated with conductive adhesive, so that the conductive adhesive can soak the thin carbon fiber felt;
[0017] (4) Sleeve: Put the dipped carbon fiber tow on the silver-plated copper clamp, and turn the clamping knob clockwise to clamp the carbon fiber bundle. When conductive glue flows from both ends of the clamp, Stop turning the knob when it's flowing.
[0018] (5) Curing: fix the clamp,...
Embodiment 2
[0020] The present invention can also operate according to the following steps:
[0021] (1) Joint stock: 8 bundles of adjacent carbon fiber filaments at the end of the carbon fiber cloth are combined into one strand;
[0022] (2) Glue coating: evenly apply conductive glue mixed with curing agent at the contact between the ply carbon fiber filament and the metal sheet; the curing agent used is dimethylimidazole, and the conductive glue is bisphenol A epoxy resin mixed with silver powder;
[0023] (3) Felt wrapping: Wrap two layers of thin carbon fiber felt on the surface of the carbon fiber filament coated with conductive adhesive, so that the conductive adhesive can soak into the thin carbon fiber felt;
[0024] (4) Sleeve: Put the dipped carbon fiber tow on the silver-plated copper clamp, and turn the clamping knob clockwise to clamp the carbon fiber bundle. When conductive glue flows from both ends of the clamp, Stop turning the knob when it's flowing.
[0025] (5) Curing...
PUM
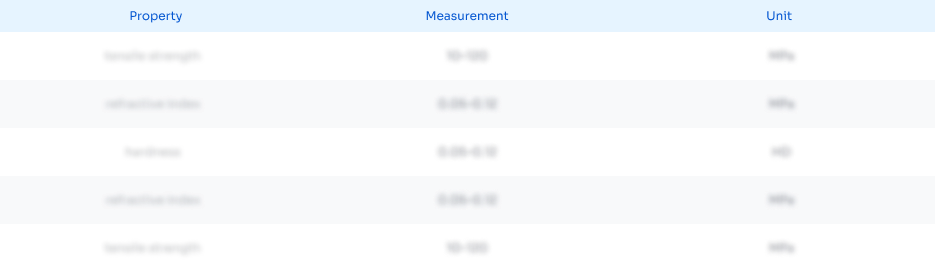
Abstract
Description
Claims
Application Information
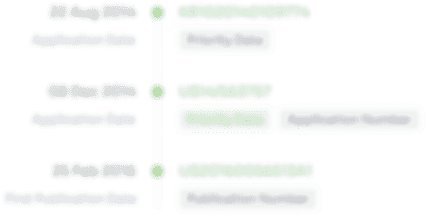
- R&D Engineer
- R&D Manager
- IP Professional
- Industry Leading Data Capabilities
- Powerful AI technology
- Patent DNA Extraction
Browse by: Latest US Patents, China's latest patents, Technical Efficacy Thesaurus, Application Domain, Technology Topic.
© 2024 PatSnap. All rights reserved.Legal|Privacy policy|Modern Slavery Act Transparency Statement|Sitemap