Composite material for ceramic sealing ring and preparation method thereof
A technology of ceramic sealing ring and composite material, applied in the field of composite material and its preparation, can solve the problems of small friction coefficient, ceramic sealing ring does not have corrosion resistance, wear resistance, thermal shock resistance, etc. The effect of reducing the coefficient and excellent corrosion resistance
- Summary
- Abstract
- Description
- Claims
- Application Information
AI Technical Summary
Benefits of technology
Problems solved by technology
Method used
Examples
specific Embodiment approach 1
[0011] Embodiment 1: The composite material of this embodiment is composed of 5-15 parts of graphite, 80-90 parts of silicon carbide and 5 parts of silicon powder by volume.
specific Embodiment approach 2
[0012] Embodiment 2: The composite material in this embodiment is composed of 50 parts of graphite, 90 parts of silicon carbide and 5 parts of silicon powder by volume. Other components and connections are the same as those in the first embodiment.
specific Embodiment approach 3
[0013] Embodiment 3: The composite material of this embodiment is composed of 15 parts of graphite, 80 parts of silicon carbide and 5 parts of silicon powder by volume. Other components and connections are the same as those in the first embodiment.
PUM
Property | Measurement | Unit |
---|---|---|
Particle size | aaaaa | aaaaa |
Mesh | aaaaa | aaaaa |
Density | aaaaa | aaaaa |
Abstract
Description
Claims
Application Information
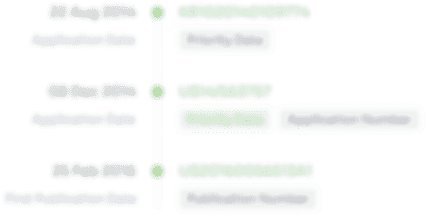
- R&D Engineer
- R&D Manager
- IP Professional
- Industry Leading Data Capabilities
- Powerful AI technology
- Patent DNA Extraction
Browse by: Latest US Patents, China's latest patents, Technical Efficacy Thesaurus, Application Domain, Technology Topic.
© 2024 PatSnap. All rights reserved.Legal|Privacy policy|Modern Slavery Act Transparency Statement|Sitemap