Preparation method of carbon-nanotube-modified polystyrene composite material
A carbon nanotube modification and polystyrene technology is applied in the field of preparation of carbon nanotube modified polystyrene composite materials, which can solve the problems that the mechanical properties of carbon nanotubes do not exert an ideal application effect, and achieve easy operation, Good dispersion and excellent mechanical properties
- Summary
- Abstract
- Description
- Claims
- Application Information
AI Technical Summary
Problems solved by technology
Method used
Examples
Embodiment 1
[0018] Prepare raw materials according to the following weight ratio: styrene 100; carbon nanotube 5; azobisisobutyronitrile 0.05; concentrated sulfuric acid 60; concentrated nitric acid 180; deionized water 100; ; 10% sodium hydroxide solution 10;
[0019] Add carbon nanotubes to a mixture of concentrated sulfuric acid and concentrated nitric acid, ultrasonically treat for 30 minutes, wash with deionized water until neutral, and dry in an oven at 80°C for 24 hours;
[0020] Mix styrene, carbon nanotubes, potassium persulfate, and sodium lauryl sulfate evenly, add 10% sodium hydroxide solution to adjust the pH value to 9, ultrasonically treat for 30 minutes, keep the temperature at 80°C, and add azobisisobutyronitrile to react After 24 hours, the reaction was completed and centrifuged until the upper layer was clear and free of impurities by adding methanol, and the product was dried in an oven at 50°C for 24 hours.
Embodiment 2
[0022] Prepare raw materials according to the following weight ratio: styrene 100; carbon nanotubes 10; benzoyl oxide 0.1; concentrated sulfuric acid 70; concentrated nitric acid 210; deionized water 120; % sodium hydroxide solution 12;
[0023] Add carbon nanotubes to a mixture of concentrated sulfuric acid and concentrated nitric acid, ultrasonically treat for 30 minutes, wash with deionized water until neutral, and dry in an oven at 80°C for 24 hours;
[0024] Mix styrene, carbon nanotubes, potassium persulfate, and sodium lauryl sulfate evenly, add 10% sodium hydroxide solution to adjust the pH value to 9, ultrasonically treat for 30 minutes, keep the temperature at 80°C, and add benzoyl oxide to react for 24 hours. At the end of the reaction, centrifuge and separate until the upper clear layer is free of impurities by adding methanol, and the product is oven-dried at 50°C for 24 hours.
Embodiment 3
[0026] Prepare raw materials according to the following weight ratio: styrene 100; carbon nanotubes 12; benzoyl oxide 0.12; concentrated sulfuric acid 80; concentrated nitric acid 240; deionized water 200; % sodium hydroxide solution 15;
[0027] Add carbon nanotubes to a mixture of concentrated sulfuric acid and concentrated nitric acid, ultrasonically treat for 30 minutes, wash with deionized water until neutral, and dry in an oven at 80°C for 24 hours;
[0028] Mix styrene, carbon nanotubes, potassium persulfate, and sodium lauryl sulfate evenly, add 10% sodium hydroxide solution to adjust the pH value to 9, ultrasonically treat for 30 minutes, keep the temperature at 80°C, and add benzoyl oxide to react for 24 hours. At the end of the reaction, centrifuge and separate until the upper clear layer is free of impurities by adding methanol, and the product is oven-dried at 50°C for 24 hours.
PUM
Property | Measurement | Unit |
---|---|---|
Tensile strength | aaaaa | aaaaa |
Impact strength | aaaaa | aaaaa |
Abstract
Description
Claims
Application Information
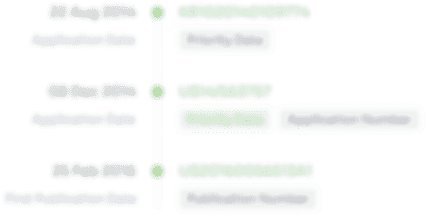
- R&D Engineer
- R&D Manager
- IP Professional
- Industry Leading Data Capabilities
- Powerful AI technology
- Patent DNA Extraction
Browse by: Latest US Patents, China's latest patents, Technical Efficacy Thesaurus, Application Domain, Technology Topic.
© 2024 PatSnap. All rights reserved.Legal|Privacy policy|Modern Slavery Act Transparency Statement|Sitemap