Production method for titanium-rich material
A production method and technology of titanium-rich materials, applied in the field of metallurgy, can solve the problems of short process flow, high cost, and high energy consumption in rotary kiln oxidation (reduction), and achieve short process flow, reduced energy consumption, and elimination of waste water discharge. Effect
- Summary
- Abstract
- Description
- Claims
- Application Information
AI Technical Summary
Benefits of technology
Problems solved by technology
Method used
Examples
Embodiment 1
[0066] Take 500g titanium concentrate (TiO 2 The grade is 47.5%) and 240g of sodium hydroxide are mixed and placed in the reactor, the control melting reaction temperature is 480 ° C, the melting reaction time is 50min, and sodium metatitanate (Na) is obtained after melting and decomposing. 2 TiO 3 ), sodium silicate, sodium manganate, sodium aluminate, sodium chromate and mixed solid phase of iron, calcium and magnesium oxides.
[0067] The obtained sodium metatitanate (Na 2 TiO 3 ) The mixed solid phase was fully washed with water, and the washing temperature was 25 °C to obtain a solid-phase hydrated sodium titanate (Na 2 O 2TiO 2 ·xH 2 O), solid phase iron, calcium, magnesium oxides and dilute lye (NaOH dilute solution containing silicon, manganese, aluminum, chromium impurities), after filtering and removing the dilute lye, carry out re-selection to remove most of iron, calcium, Magnesium oxide.
[0068] In the mixed solid phase of hydrated sodium titanate and the rem
Embodiment 2
[0072] Take 500g titanium concentrate (TiO 2 The grade is 47.5%) and 240g of sodium hydroxide are mixed and placed in the reactor, the control melting reaction temperature is 500 ° C, the melting reaction time is 60min, and sodium metatitanate (Na) is obtained after melting and decomposing. 2 TiO 3 ), sodium silicate, sodium manganate, sodium aluminate, sodium chromate and mixed solid phase of iron, calcium and magnesium oxides.
[0073] The obtained sodium metatitanate (Na 2 TiO 3 ) The mixed solid phase was fully washed with water, and the washing temperature was 30 °C to obtain solid-phase hydrated sodium titanate (Na 2 O 2TiO 2 ·xH 2 O), solid-phase iron, calcium, magnesium oxides and dilute lye (NaOH dilute solution containing silicon, manganese, aluminum, and chromium impurities), after filtration to remove the dilute lye, re-selection is performed to remove most of the iron, calcium, Magnesium oxide.
[0074] In the mixed solid phase of hydrated sodium titanate and
Embodiment 3
[0078] Take 500g titanium concentrate (TiO 2 The grade is 47.5%) and 240g of sodium hydroxide are mixed and placed in the reactor, the control melting reaction temperature is 550 ° C, the melting reaction time is 70min, and sodium metatitanate (Na) is obtained after melting and decomposing. 2 TiO 3 ), sodium silicate, sodium manganate, sodium aluminate, sodium chromate and mixed solid phase of iron, calcium and magnesium oxides.
[0079] The obtained sodium metatitanate (Na 2 TiO 3 ) The mixed solid phase was fully washed with water, and the washing temperature was 40 °C to obtain a solid-phase hydrated sodium titanate (Na 2 O 2TiO 2 ·xH 2 O), solid-phase iron, calcium, magnesium oxides and dilute lye (NaOH dilute solution containing silicon, manganese, aluminum, and chromium impurities), after filtration to remove the dilute lye, re-selection is performed to remove most of the iron, calcium, Magnesium oxide.
[0080] In the mixed solid phase of hydrated sodium titanate an
PUM
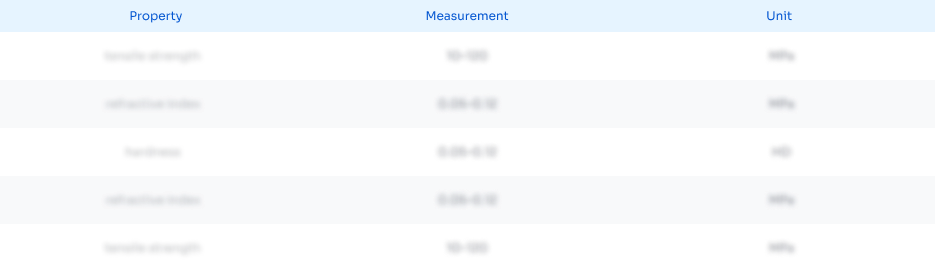
Abstract
Description
Claims
Application Information
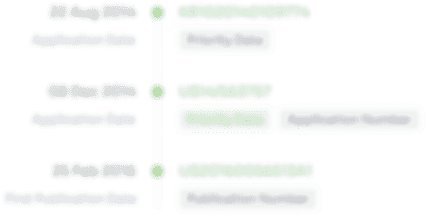
- R&D Engineer
- R&D Manager
- IP Professional
- Industry Leading Data Capabilities
- Powerful AI technology
- Patent DNA Extraction
Browse by: Latest US Patents, China's latest patents, Technical Efficacy Thesaurus, Application Domain, Technology Topic.
© 2024 PatSnap. All rights reserved.Legal|Privacy policy|Modern Slavery Act Transparency Statement|Sitemap