Method for making coated filter cloth through wet process
A filter cloth and film coating technology, which is applied in the field of wet manufacturing of film-coated filter cloth, can solve the problems of uneven distribution of pores of membrane materials, difficulty in adjusting and controlling porosity, affecting product quality, etc., to achieve good hydrophobicity and improve filtration. Efficiency, the effect of reducing energy consumption
- Summary
- Abstract
- Description
- Claims
- Application Information
AI Technical Summary
Benefits of technology
Problems solved by technology
Method used
Image
Examples
Embodiment Construction
[0014] The embodiments of the present invention are described in detail below, and the embodiments are only used to explain the present invention, but not to be construed as limiting the present invention. Follow the process described in the accompanying drawings, select the woven filter cloth (1 in the figure) as the filter cloth to be coated, the fiber raw material of this filter cloth is polypropylene filament, its warp and weft fineness is 750D, and its warp and weft density is 160pcs / 10CM, the weave is plain weave. Because the fineness of the fibers constituting the filter cloth is very large, the surface of the filter cloth is uneven. Therefore, the surface of the film must be calendered before the film is applied to make the surface of the film material smooth and flat. , so that the resulting film is uniform and smooth. The calender (3 in the figure) selects a combination of metal smooth roll and nylon smooth roll for calendering, the maximum theoretical pressure is 80
PUM
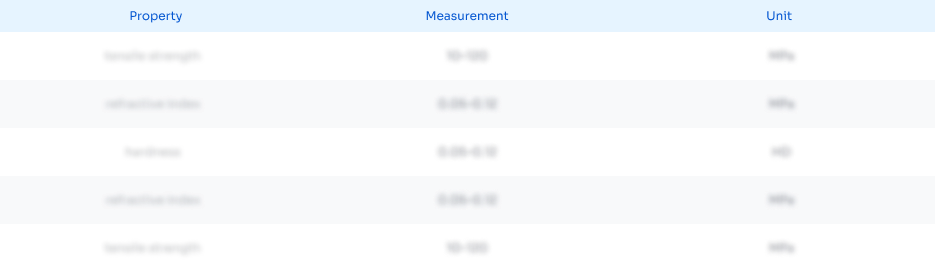
Abstract
Description
Claims
Application Information
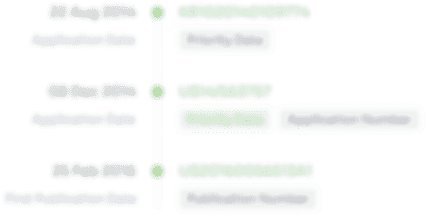
- R&D Engineer
- R&D Manager
- IP Professional
- Industry Leading Data Capabilities
- Powerful AI technology
- Patent DNA Extraction
Browse by: Latest US Patents, China's latest patents, Technical Efficacy Thesaurus, Application Domain, Technology Topic.
© 2024 PatSnap. All rights reserved.Legal|Privacy policy|Modern Slavery Act Transparency Statement|Sitemap