Gear chamber cover and preparation method thereof
A technology of gear chamber cover and weight percentage, applied in the field of auto parts, can solve the problem of short service life of the gear chamber cover, and achieve the effects of improving strength, saving costs and long service life
- Summary
- Abstract
- Description
- Claims
- Application Information
AI Technical Summary
Benefits of technology
Problems solved by technology
Method used
Examples
Embodiment 1
[0020] A gear chamber cover, comprising the following chemical composition in weight percentage: C3.6%, Si1.75%, Mn0.5%, S0.03%, P0.5%, and the balance is iron.
[0021] The preparation method of the gear chamber cover includes the following sequential steps:
[0022] (1) use water glass, red clay and sandy soil to prepare sand mold;
[0023] (2) Ironmaking: Add clean and dry ordinary steel scrap, pig iron, and carbon-increasing waste electrodes into the furnace, heat and melt, raise the temperature to 1550°C, and add preheated ferromanganese and ferrosilicon 10 minutes before tapping Carry out precipitation deoxidation and adjust the composition;
[0024] (3) Casting molding: Slag removal is performed on the molten iron once, and then the molten iron is poured into the ingot mold. The pouring temperature of the molten steel is 1350°C. The pouring is first slow, medium fast, and then fine;
[0025] (4) Mold removal and sand cleaning: open the mold after cooling for 6 hours, sep
Embodiment 2
[0028] A gear chamber cover, comprising the following chemical composition by weight percentage: C3.8%, Si1.9%, Mn00.6%, S0.05%, P0.10%, and the balance is iron.
[0029] The preparation method of the gear chamber cover includes the following sequential steps:
[0030] (1) use water glass, red clay and sandy soil to prepare sand mold;
[0031] (2) Ironmaking: Add clean and dry ordinary steel scrap, pig iron, and carbon-increasing waste electrodes into the furnace, heat and melt, raise the temperature to 1500°C, and add preheated ferromanganese and ferrosilicon 10 minutes before tapping Carry out precipitation deoxidation and adjust the composition;
[0032] (3) Casting molding: Slag removal is performed on the molten iron once, and then the molten iron is poured into the ingot mold. The pouring temperature of the molten steel is 1300°C, and the pouring is first slow, medium fast, and then fine;
[0033] (4) Mold removal and sand cleaning: open the mold after cooling for 3 hours
Embodiment 3
[0036] A gear chamber cover comprises the following chemical components in weight percentage: C3.5%, Si1.6%, Mn0.1%, and the balance is iron.
[0037] The preparation method of the gear chamber cover includes the following sequential steps:
[0038] (1) use water glass, red clay and sandy soil to prepare sand mold;
[0039] (2) Ironmaking: Add clean and dry ordinary steel scrap, pig iron, and carbon-increasing waste electrodes into the furnace, heat and melt, raise the temperature to 1530°C, and add preheated ferromanganese and ferrosilicon 10 minutes before tapping Carry out precipitation deoxidation and adjust the composition;
[0040] (3) Casting molding: Slag removal is performed on the molten iron once, and then the molten iron is poured into the ingot mold. The pouring temperature of the molten steel is 1330°C. The pouring is first slow, medium fast, and then fine;
[0041] (4) Mold removal and sand cleaning: open the mold after cooling for 4 hours, separate and finely gr
PUM
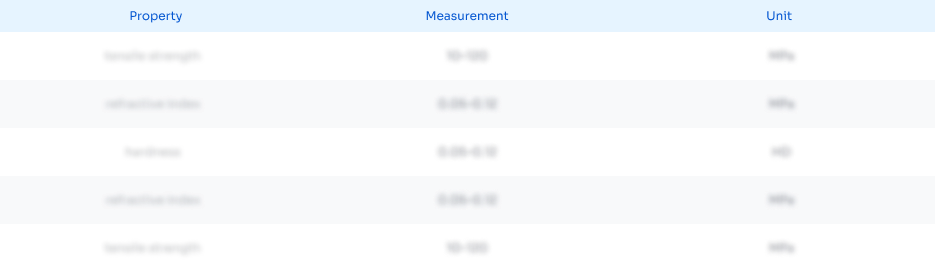
Abstract
Description
Claims
Application Information
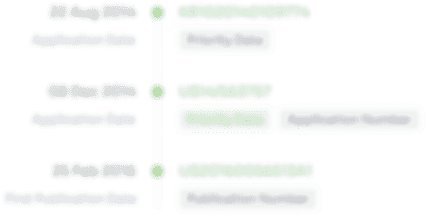
- R&D Engineer
- R&D Manager
- IP Professional
- Industry Leading Data Capabilities
- Powerful AI technology
- Patent DNA Extraction
Browse by: Latest US Patents, China's latest patents, Technical Efficacy Thesaurus, Application Domain, Technology Topic.
© 2024 PatSnap. All rights reserved.Legal|Privacy policy|Modern Slavery Act Transparency Statement|Sitemap