Colorful acid and alkali resistant laser printing ink and preparation method thereof
A printing ink, acid and alkali resistance technology, applied in the field of printing ink, can solve the problems of poor acid and alkali resistance, affecting the yield of production, extinction, etc., to achieve the effect of rich colors and increase acid and alkali resistance
- Summary
- Abstract
- Description
- Claims
- Application Information
AI Technical Summary
Problems solved by technology
Method used
Image
Examples
Embodiment 1
[0022] 1) Weigh 10 parts of methyl ethyl ketone and 20 parts of isopropanol into the container, stir at a speed of 700r / min for 20min, and disperse evenly;
[0023] 2) Weigh 25 parts of diphenolic propane type epoxy resin with a solid content of 30wt% and an average molecular weight of 500, add the dispersed solvent, stir at a speed of 1500r / min for 60min, and then disperse evenly;
[0024] 3) Weigh 10 parts of 120 red toner and slowly add to the above mixed solution, while stirring at the speed of 1000r / min, stir for 20 minutes to make the dispersion even; then add the mixed solution to the sand mill and grind for 45 minutes , the temperature is controlled at 50~60℃ until the fineness is ≤10μm;
[0025] 4) Weigh 2 parts of ethylene bis stearic acid amide and add it to the ground solution, stir at a speed of 1000r / min for 30min, disperse evenly, and obtain the color acid and alkali resistant laser printing ink.
Embodiment 2
[0027] 1) Weigh 10 parts of methyl ethyl ketone and 20 parts of isopropanol into the container, stir at a speed of 700r / min for 20min, and disperse evenly;
[0028] 2) Weigh 25 parts of diphenolic propane type epoxy resin with a solid content of 40wt% and an average molecular weight of 340, add the dispersed solvent, stir at a speed of 800r / min for 45min, and then disperse evenly;
[0029] 3) Weigh 10 parts of 120 purple toner and slowly add to the above mixed solution, stir while adding, the rotation speed is 1500r / min, stir for 30min to make the dispersion even; then add the mixed solution into the sand mill, grind for 30min , the temperature is controlled at 50~60℃ until the fineness is ≤10μm;
[0030] 4) Weigh 3 parts of ethylene bis stearic acid amide and add to the ground solution, stir at 800r / min for 45min, disperse evenly, and obtain the color acid and alkali resistant laser printing ink.
Embodiment 3
[0032] 1) Weigh 30 parts of butanone and 10 parts of isopropanol into the container, stir at 1000r / min for 30min, and disperse evenly;
[0033] 2) Weigh 30 parts of diphenolic propane type epoxy resin with a solid content of 50wt% and an average molecular weight of 380, add the dispersed solvent, stir at a speed of 1000r / min for 80min, and then disperse evenly;
[0034] 3) Weigh 15 parts of 120 blue toner and slowly add the above mixed solution, and stir while adding at a speed of 1200r / min, stir for 45 minutes to make the dispersion even; then add the mixed solution to a sand mill and grind for 60 minutes , the temperature is controlled at 50~60℃ until the fineness is ≤10μm;
[0035] 4) Weigh 6 parts of ethylene bis stearic acid amide and add it to the ground solution, stir at a speed of 1200r / min for 60min, disperse evenly, and obtain the color acid and alkali resistant laser printing ink.
PUM
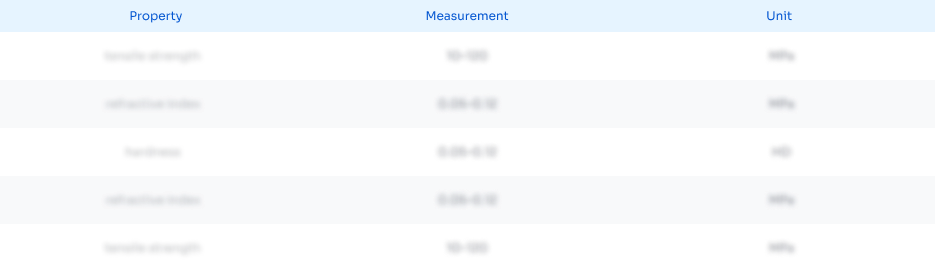
Abstract
Description
Claims
Application Information
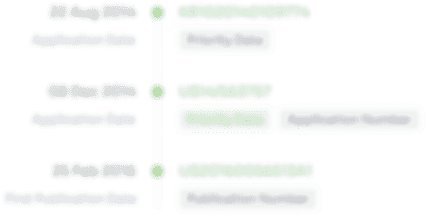
- R&D Engineer
- R&D Manager
- IP Professional
- Industry Leading Data Capabilities
- Powerful AI technology
- Patent DNA Extraction
Browse by: Latest US Patents, China's latest patents, Technical Efficacy Thesaurus, Application Domain, Technology Topic.
© 2024 PatSnap. All rights reserved.Legal|Privacy policy|Modern Slavery Act Transparency Statement|Sitemap