Solution preparation method for producing electrolytic manganese or manganese dioxide from low-grade manganese oxide ores
A technology of manganese oxide ore and manganese dioxide, which is applied in the field of manganese mineral smelting, can solve the problems of slow leaching speed, system acid expansion, acid expansion, etc., and achieve the effects of acid balance, reduced acid consumption, and low cost
- Summary
- Abstract
- Description
- Claims
- Application Information
AI Technical Summary
Problems solved by technology
Method used
Image
Examples
Embodiment 1
[0036] Take 100g of manganese oxide ore powder with a manganese content of 25% and mix it with electrolytic manganese anolyte, leaching at 50°C for 1 hour, and filter to obtain presoak solution and presoak slag with 15% water content; Add lignite powder and mix well, then add 35g of concentrated sulfuric acid with a concentration of 95% and mix well, react with self-heating to a maximum temperature of 250°C and then mature for 2 hours, then use the above presoaking liquid to leach the cured material, the leaching temperature is 95°C, The leaching time is 60min, and the manganese leaching rate is 98.5%. The leached ore pulp is oxidized with manganese oxide ore powder, and rhodochrosite powder is used as a neutralizing agent to carry out oxidation neutralization and iron removal, after oxidation and neutralization, use a vulcanizing agent to remove heavy metal ions in the manganese sulfate solution, and then add an appropriate amount of electrolytic additives After the manganese me
Embodiment 2
[0038] Take 100g of manganese oxide ore powder with a manganese content of 15% and mix it with the electrolytic manganese anolyte, leaching at 90°C for 2 hours, and filter to obtain a presoak solution and a prepreg slag with a water content of 10%; Add bituminous coal powder and mix well, then add 30g of concentrated sulfuric acid with a concentration of 95% and mix well, react with self-heating to a maximum temperature of 150°C, and then mature for 2 hours, then use the above presoaking liquid to leaching the matured material, the leaching temperature is 30°C , leaching time 1h, manganese leaching rate 95.5%. The leached ore pulp is oxidized with manganese oxide ore powder, and rhodochrosite powder is used as a neutralizing agent to carry out oxidation neutralization and iron removal, after oxidation and neutralization, use a vulcanizing agent to remove heavy metal ions in the manganese sulfate solution, and then add an appropriate amount of electrolytic additives After the mang
Embodiment 3
[0040] Take 100g of manganese oxide ore powder with a manganese content of 25% and mix it with the electrolytic manganese dioxide anolyte, leaching for 1 hour at 50°C, and filter to obtain the presoak solution and prepreg slag with a water content of 15%; Add lignite powder at 5% and mix well, then add 35g of concentrated sulfuric acid with a concentration of 95% and mix well, react with self-heating to a maximum temperature of 250°C and then mature for 2 hours, then use the above presoaking liquid to leach the cured material at a temperature of 95 ℃, the leaching time is 60min, and the manganese leaching rate is 98.5%. The leached ore pulp is oxidized with manganese oxide ore powder, and rhodochrosite powder is used as a neutralizing agent to carry out oxidation neutralization and iron removal, after oxidation and neutralization, use a vulcanizing agent to remove heavy metal ions in the manganese sulfate solution, and then add an appropriate amount of electrolytic additives Afte
PUM
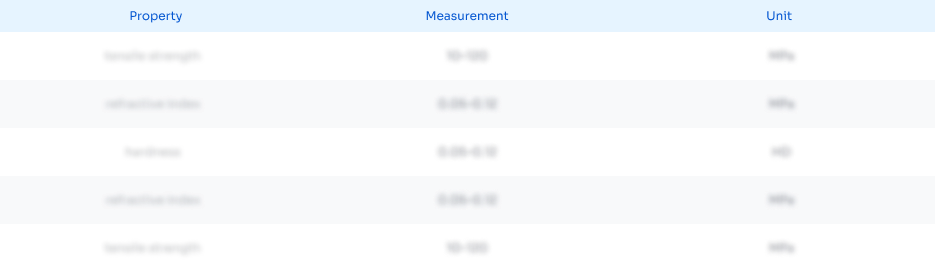
Abstract
Description
Claims
Application Information
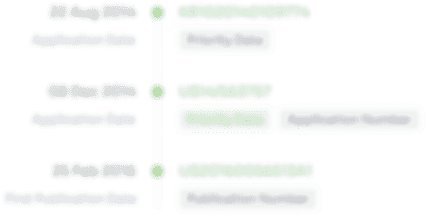
- R&D Engineer
- R&D Manager
- IP Professional
- Industry Leading Data Capabilities
- Powerful AI technology
- Patent DNA Extraction
Browse by: Latest US Patents, China's latest patents, Technical Efficacy Thesaurus, Application Domain, Technology Topic.
© 2024 PatSnap. All rights reserved.Legal|Privacy policy|Modern Slavery Act Transparency Statement|Sitemap