Method for preparing CPVC resin filling agent by adopting ardealite
A technology of CPVC resin and phosphogypsum, which is applied in the field of preparing CPVC resin fillers, and achieves the effects of obvious economical practicability, cost reduction and treatment cost reduction
- Summary
- Abstract
- Description
- Claims
- Application Information
AI Technical Summary
Benefits of technology
Problems solved by technology
Method used
Examples
Embodiment 1
[0025] The impurity removal treatment is carried out on the phosphogypsum, and the weight percentage of impurities contained in the phosphogypsum is controlled to 4%. React phosphogypsum with excess sodium carbonate, filter, wash and dry to obtain calcium carbonate. Calcium carbonate, the by-product potato dregs obtained after starch extraction from potatoes, α-amylase, and okara obtained from the production of soybean milk are placed in a fermentation container at a mass ratio of 0.3:2:0.02:1, and lactic acid bacteria are added to the fermentation container, and stirred evenly , anaerobic fermentation at 38°C for 40 hours, and lactic acid was obtained after separation and purification; the number of live lactic acid bacteria contained 4 million per gram of potato dregs; in terms of mass fraction, the starch content of potato dregs was 33%; On a fractional basis, okara contains 15% protein. Mix the obtained lactic acid and stearic acid in a molar ratio of 1:2 and put them into a
Embodiment 2
[0027] Perform impurity removal treatment on the phosphogypsum, and control the weight percentage of impurities contained in the phosphogypsum to 3%. React phosphogypsum with excess sodium carbonate, filter, wash and dry to obtain calcium carbonate. Calcium carbonate, the by-product potato dregs after starch extraction from potatoes, α-amylase, and the bean dregs obtained from producing tofu are placed in a fermentation container in a mass ratio of 0.4:2.5:0.025:1.5, and lactic acid bacteria are added to the fermentation container, and stirred evenly. Anaerobic fermentation at 40°C for 32 hours, separation and purification to obtain lactic acid; the number of viable lactic acid bacteria per gram of potato residue is 4.5 million; in terms of mass fraction, the starch content of potato residue is 37%; Calculated, okara contains 16% protein. Mix the obtained lactic acid and stearic acid in a molar ratio of 1:2.5 and put them into a three-neck bottle with a stirrer, add hardened oil
Embodiment 3
[0029] The impurity removal treatment is carried out on the phosphogypsum, and the weight percentage of impurities contained in the phosphogypsum is controlled to 2%. React phosphogypsum with excess sodium carbonate, filter, wash and dry to obtain calcium carbonate. Calcium carbonate, the by-product potato dregs after starch extraction from potatoes, α-amylase, and the bean dregs obtained from producing tofu are placed in a fermentation container in a mass ratio of 0.5:3:0.03:2, and lactic acid bacteria are added to the fermentation container, and stirred evenly. Anaerobic fermentation at 45°C for 20 hours, separation and purification to obtain lactic acid; the number of viable lactic acid bacteria per gram of potato residue is 5 million; in terms of mass fraction, the sugar content of potato residue and α-amylase is 40 %; In terms of mass fraction, okara contains 22% protein. Mix the obtained lactic acid and stearic acid in a molar ratio of 1:3 and put them into a three-necked
PUM
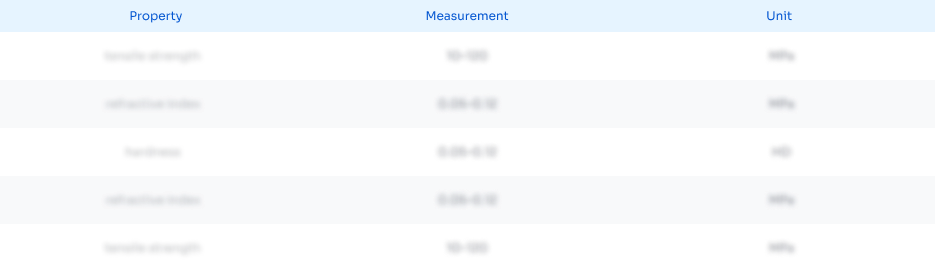
Abstract
Description
Claims
Application Information
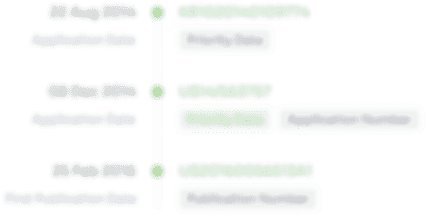
- R&D Engineer
- R&D Manager
- IP Professional
- Industry Leading Data Capabilities
- Powerful AI technology
- Patent DNA Extraction
Browse by: Latest US Patents, China's latest patents, Technical Efficacy Thesaurus, Application Domain, Technology Topic.
© 2024 PatSnap. All rights reserved.Legal|Privacy policy|Modern Slavery Act Transparency Statement|Sitemap