Epoxy resin based on uracil and preparation method and application thereof
A technology of epoxy resin and uracil, applied in the field of material science, can solve the problems that the performance is difficult to meet the actual requirements, and the price of thermosetting resin is high, and achieve the effect of easy industrialization, high heat resistance and mechanical strength, and strong operability.
- Summary
- Abstract
- Description
- Claims
- Application Information
AI Technical Summary
Benefits of technology
Problems solved by technology
Method used
Image
Examples
Embodiment 1
[0034] Mix 112 grams of uracil and 1116 grams of epichlorohydrin, raise the temperature to 85°C, add 5 grams of tetramethylammonium chloride, react for 1.5 hours and then cool down to 30°C, then add 300 grams of 30wt% sodium hydroxide dropwise , After 1h dripping, continue to react for 3h. After the reaction system was lowered to room temperature, it was washed with 200 mL of deionized water each time for a total of 4 times, and then the solvent was removed with a rotary evaporator, and vacuum-dried at 50°C for 12 hours to obtain a light yellow transparent viscous liquid, which is a uracil-based ring Oxygen resin 210 grams, productive rate is 94.5%.
[0035] The above-mentioned epoxy resin based on uracil is carried out structural identification, and the infrared spectrogram is as follows figure 1 shown. The identification result is: there is 3050cm in the infrared spectrum -1 、2960cm -1 、2930cm -1 、2850cm -1 、1698cm -1 、1648cm -1 、1460cm -1 、1380cm -1 、1250cm -1 、820c
Embodiment 2
[0039] Mix 112 grams of uracil and 700 grams of epibromohydrin, raise the temperature to 110°C, add 20 grams of octadecyltrimethylammonium bromide, react for 0.5 hours and cool down to 30°C, then add dropwise 35% hydroxide Potassium solution 300 grams, dripped in 1 hour, continued to react at 30°C for 3 hours. After the reaction system was lowered to room temperature, it was washed with 200 mL of deionized water each time for a total of 4 times, and then the solvent was removed with a rotary evaporator, and vacuum-dried at 50°C for 12 hours to obtain 217 grams of uracil-based epoxy resin. The yield was was 97.5%.
[0040] The structure of the uracil-based epoxy resin obtained above was identified, and the identification result was basically the same as that in Example 1. The measured epoxy value is 0.91 epoxy equivalent / 100 grams of resin. 100 parts by weight of the uracil-based epoxy resin and 55 parts by weight of hexahydrophthalic anhydride were mixed, and 0.5 parts by weigh
Embodiment 3
[0042] Mix 112 grams of uracil and 800 grams of epichlorohydrin, raise the temperature to 90°C, add 12 grams of hexamethylenetetraammonium, react at 60°C for 1 hour, then cool down to 30°C, then dropwise add 35% hydrogen Potassium oxide solution 300 grams, dripped in 1 hour, continued reaction at 30°C for 3 hours. After the reaction system was cooled to room temperature, it was washed with 200 mL of deionized water each time for a total of 4 times, and then the solvent was removed by a rotary evaporator, and vacuum-dried at 50° C. for 12 hours to obtain 210 grams of uracil-based epoxy resin.
[0043] The uracil-based epoxy resin obtained above was identified, and the identification result was basically the same as that in Example 1. The measured epoxy value is 0.92 epoxy equivalent / 100 grams of resin. 100 parts by weight of the uracil-based epoxy resin and 41 parts by weight of hexahydrophthalic anhydride were mixed, and 0.5 parts by weight of imidazole was added. Then cured
PUM
Property | Measurement | Unit |
---|---|---|
Flexural modulus | aaaaa | aaaaa |
Bending strength | aaaaa | aaaaa |
Flexural modulus | aaaaa | aaaaa |
Abstract
Description
Claims
Application Information
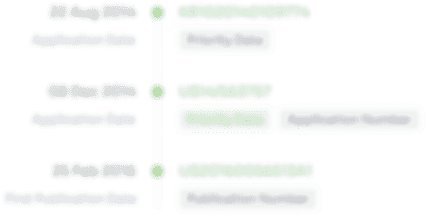
- R&D Engineer
- R&D Manager
- IP Professional
- Industry Leading Data Capabilities
- Powerful AI technology
- Patent DNA Extraction
Browse by: Latest US Patents, China's latest patents, Technical Efficacy Thesaurus, Application Domain, Technology Topic.
© 2024 PatSnap. All rights reserved.Legal|Privacy policy|Modern Slavery Act Transparency Statement|Sitemap