OPP (oriented polypropylene) heat dissipating and insulating release film
A technology of release film and thin film layer, which is applied in the field of OPP heat dissipation and insulating release film, can solve the problems of poor weather resistance of OPP film, affect the scope of use, single performance, etc., achieve diversified functions, improve the scope of use, and good compatibility Effect
- Summary
- Abstract
- Description
- Claims
- Application Information
AI Technical Summary
Benefits of technology
Problems solved by technology
Method used
Examples
Embodiment 1
[0048] A kind of OPP heat dissipation insulation release film, comprises thin film layer, and described thin film layer comprises following component by weight ratio:
[0049] OPP: 100 copies;
[0050] Porcelain powder: 6 parts;
[0051] Epoxy resin 6101: 5 parts;
[0052] Furfuryl alcohol furfural resin: 5 parts;
[0053] Melamine: 1 part;
[0054] Polyacrylamide: 1.2 parts;
[0055] Polyamide 66: 4 parts;
[0056] Nano alumina: 1.2 parts;
[0057] Mica powder: 2 parts;
[0058] Talcum powder: 1.2 parts;
[0059] Polyvinyl alcohol tert-butyraldehyde: 2 parts;
[0060] PFA: 5 parts;
[0061] PBT: 8 parts;
[0062] PET: 10 copies;
[0063] Polyethylene glycol monomethyl ether: 15 parts;
[0064] PTFE: 8 parts;
[0065] Polymethyl methacrylate: 8 parts;
[0066] Polyphenylene sulfide: 4 parts;
[0067] Fiberglass: 4 parts;
[0068] Organic montmorillonite: 4 parts;
[0069] Paraffin: 6 parts;
[0070] Polyether ether ketone fiber: 2 parts;
[0071] nano-SiO 2 :3
Embodiment 2
[0079] A kind of OPP heat dissipation insulation release film, comprises thin film layer, and described thin film layer comprises following component by weight ratio:
[0080] OPP: 110 copies;
[0081] Porcelain powder: 7 parts;
[0082] Epoxy resin 6101: 6 parts;
[0083] Furfuryl alcohol furfural resin: 6 parts;
[0084] Melamine: 1.5 parts;
[0085] Polyacrylamide: 1.4 parts;
[0086] Polyamide 66: 5 parts;
[0087] Nano alumina: 1.4 parts;
[0088] Mica powder: 3 parts;
[0089] Talcum powder: 1.3 parts;
[0090] Polyvinyl alcohol tert-butyraldehyde: 3 parts;
[0091] PFA: 6 parts;
[0092] PBT: 9 parts;
[0093] PET: 11 parts;
[0094] Polyethylene glycol monomethyl ether: 18 parts;
[0095] PTFE: 9 parts;
[0096] Polymethyl methacrylate: 9 parts;
[0097] Polyphenylene sulfide: 5 parts;
[0098] Fiberglass: 5 parts;
[0099] Organic montmorillonite: 5 parts;
[0100] Paraffin: 7 parts;
[0101] Polyether ether ketone fiber: 3 parts;
[0102] nano-SiO 2 :4
Embodiment 3
[0110] A kind of OPP heat dissipation insulation release film, comprises thin film layer, and described thin film layer comprises following component by weight ratio:
[0111] OPP: 120 copies;
[0112] Porcelain powder: 8 parts;
[0113] Epoxy resin 6101: 7 parts;
[0114] Furfuryl alcohol furfural resin: 7 parts;
[0115] Melamine: 2 parts;
[0116] Polyacrylamide: 1.6 parts;
[0117] Polyamide 66: 6 parts;
[0118] Nano alumina: 1.6 parts;
[0119] Mica powder: 4 parts;
[0120] Talcum powder: 1.4 parts;
[0121] Polyvinyl alcohol tert-butyraldehyde: 4 parts;
[0122] PFA: 7 parts;
[0123] PBT: 10 copies;
[0124] PET: 12 copies;
[0125] Polyethylene glycol monomethyl ether: 20 parts;
[0126] PTFE: 10 parts;
[0127] Polymethyl methacrylate: 10 parts;
[0128] Polyphenylene sulfide: 6 parts;
[0129] Fiberglass: 6 parts;
[0130] Organic montmorillonite: 6 parts;
[0131] Paraffin: 8 parts;
[0132] PEEK fiber: 4 parts;
[0133] nano-SiO 2 : 5 copies;
PUM
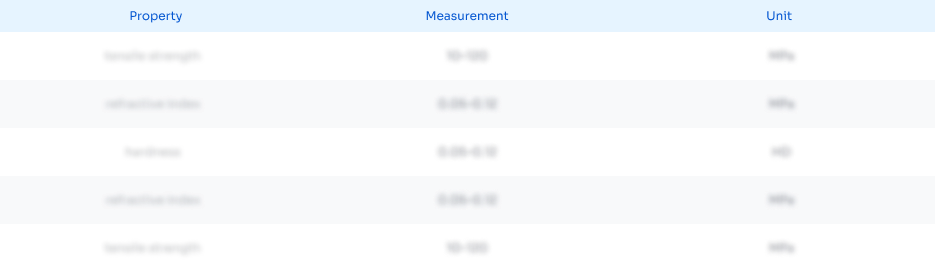
Abstract
Description
Claims
Application Information
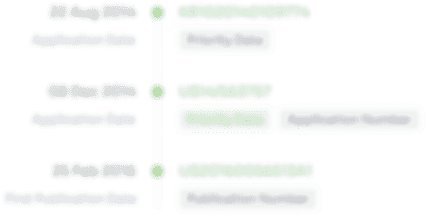
- R&D Engineer
- R&D Manager
- IP Professional
- Industry Leading Data Capabilities
- Powerful AI technology
- Patent DNA Extraction
Browse by: Latest US Patents, China's latest patents, Technical Efficacy Thesaurus, Application Domain, Technology Topic.
© 2024 PatSnap. All rights reserved.Legal|Privacy policy|Modern Slavery Act Transparency Statement|Sitemap