Preparation method for Nb-Zr alloy/Cu multi-core composite wire
A technology of composite wire and alloy wire, which is applied in the direction of cable/conductor manufacturing, electrical components, circuits, etc., can solve the problems of shortened wire life, easy corrosion and oxidation of core wire, etc., and achieves reduced composite times, good compactness, and not easy to twist and sliding effect
- Summary
- Abstract
- Description
- Claims
- Application Information
AI Technical Summary
Benefits of technology
Problems solved by technology
Method used
Examples
Embodiment 1
[0025] The preparation method of the present embodiment Nb-Zr alloy / Cu multi-core composite wire comprises the following steps:
[0026] Step 1. Melting and pouring: Mix Nb and Zr evenly at a mass ratio of 100:4, place them in the crucible of an arc induction furnace, melt for 3 hours at a temperature of 2500°C, and pour them under water bath cooling conditions after the two are fully melted Shaped to obtain a Nb-Zr alloy ingot with a cross-sectional diameter of 120 mm; the Nb and Zr are solid raw materials, and the Nb in this embodiment is preferably allocated in the form of Nb blocks, Nb particles or Nb powder. Zr is preferably added in the form of Zr blocks, Zr granules or Zr powder, and the casting time is 40s;
[0027] Step 2, hot extrusion: heat the Nb-Zr alloy ingot described in step 1 at a temperature of 800° C. for 4 hours, and then carry out extrusion processing under the condition of an extrusion ratio of 9 to obtain a cross-sectional diameter of 40mm Nb-Zr alloy ba
Embodiment 2
[0034] The preparation method of the present embodiment Nb-Zr alloy / Cu multi-core composite wire comprises the following steps:
[0035] Step 1. Melting and pouring: Mix Nb and Zr evenly at a mass ratio of 100:5, place them in the crucible of an arc induction furnace, and melt them at a temperature of 2500°C for 2.5 hours. After the two are fully melted, cool them in a water bath Casting molding to obtain a Nb-Zr alloy ingot with a cross-sectional diameter of 100mm; the Nb and Zr are both solid raw materials, and the Nb described in this embodiment is preferably allocated in the form of Nb blocks, Nb granules or Nb powder. The Zr is preferably added in the form of Zr blocks, Zr granules or Zr powder, and the casting time is 35s;
[0036] Step 2, hot extrusion: heat the Nb-Zr alloy ingot described in step 1 at a temperature of 700°C for 3.5 hours, and then carry out extrusion processing under the condition of an extrusion ratio of 9.8 to obtain a cross-sectional diameter 32mm N
Embodiment 3
[0043] The preparation method of the present embodiment Nb-Zr alloy / Cu multi-core composite wire comprises the following steps:
[0044] Step 1. Melting and pouring: Mix Nb and Zr evenly at a mass ratio of 100:6, place them in the crucible of an arc induction furnace, melt for 2 hours at a temperature of 2500°C, and pour them under water bath cooling conditions after the two are fully melted Shaped to obtain a Nb-Zr alloy ingot with a cross-sectional diameter of 80 mm; the Nb and Zr are solid raw materials, and the Nb in this embodiment is preferably allocated in the form of Nb blocks, Nb granules or Nb powder. Zr is preferably added in the form of Zr blocks, Zr particles or Zr powder, and the casting time is 50s;
[0045] Step 2, hot extrusion: heat the Nb-Zr alloy ingot described in step 1 at a temperature of 700° C. for 6 hours, and then carry out extrusion processing under the condition of an extrusion ratio of 8.4 to obtain a cross-sectional diameter of 28mm Nb-Zr alloy b
PUM
Property | Measurement | Unit |
---|---|---|
Cross section diameter | aaaaa | aaaaa |
Diameter | aaaaa | aaaaa |
Outer diameter | aaaaa | aaaaa |
Abstract
Description
Claims
Application Information
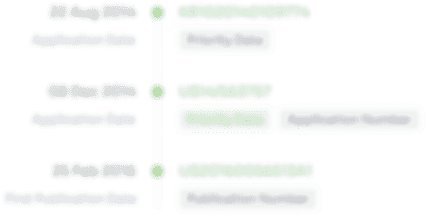
- R&D Engineer
- R&D Manager
- IP Professional
- Industry Leading Data Capabilities
- Powerful AI technology
- Patent DNA Extraction
Browse by: Latest US Patents, China's latest patents, Technical Efficacy Thesaurus, Application Domain, Technology Topic.
© 2024 PatSnap. All rights reserved.Legal|Privacy policy|Modern Slavery Act Transparency Statement|Sitemap